
2022-Korea-Showcase-Syzygy-Plasmonics
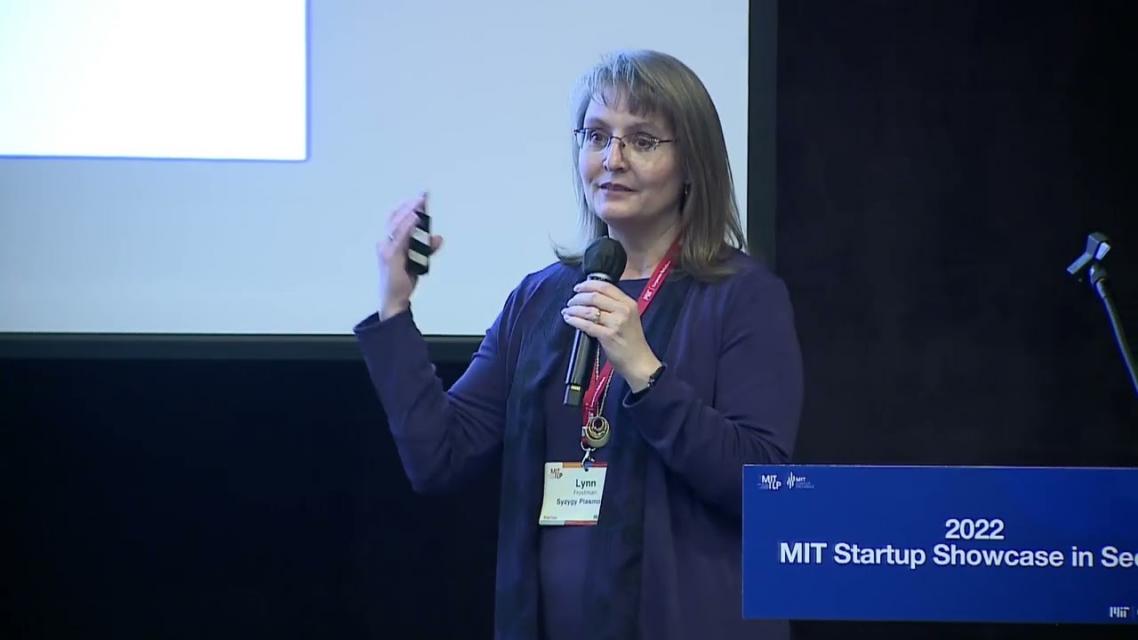
-
Interactive transcript
[APPLAUSE]
SPEAKER: [KOREAN SPEECH]
LYNN FROSTMAN: Good afternoon. It's my pleasure to tell you a little bit more about Syzygy Plasmonics today. My name is Lynn Frostmann, and we are electrifying the chemical industry.
We basically have a way to run chemical reactions with light instead of heat, and thereby reduce both emissions and cost. And we're proud to be affiliated with MIT as one of The Engine's member companies.
So this is a pretty simplified view of the chemical industry that we're targeting. But the main take-home message is that there are several key intermediate molecules that make up a vast majority of the end use products or go into them. So if you want to have an impact on the sustainability of the chemical industry, focusing on these intermediate molecules is a great way to get the maximum amount of impact.
And the challenge in the chemical industry is that many of the reactions are powered by catalysts. And those catalysts need heat to operate. And that heat is typically generated by the combustion of fossil fuels right now.
Those combustion processes contribute about a gigaton of CO2 emissions every year right now. And this is a very difficult challenge to solve to help decarbonize the chemical industry. What we're bringing to the table is a new type of reactor. It works with LED lights instead of with heat.
And that allows us to fully electrify the chemical reaction process, and thereby reducing the emissions. This is based on two basic sets of innovations, one around the photocatalyst. It is the world's most stable and active photocatalyst. It's the result of 30 years of research at Rice University that has now been commercialized by Syzygy.
And the great thing about this-- it is a platform technology. So we can look at many different types of chemical reactions with these different catalysts. And we are starting with a couple of key ones.
One is looking at the decomposition of ammonia to give hydrogen. The other is looking at dry methane reforming, which allows you to take methane and CO2 and convert those into SYN gas, which then can be used to produce synthetic fuels and methanol. But because we have to run our reactors with light, we had to create a whole new type of chemical reactor.
So we build our reactors out of glass, and regular stainless steel, and some aluminum, and some plastics. And because we're able to use these more commodity-type of materials, it allows us to lower the cost of the chemical reactors. We don't need any hastelloy in there. We operate at much lower temperatures, much lower pressures.
So let's talk about a specific use case. As many of you may have heard, there's a lot of folks interested in hydrogen right now as one of the transition fuels. And in order to make hydrogen and transport it-- transporting is actually one of the bigger challenges.
So there's a lot of people who are looking at this idea of using ammonia as that transport carrier. How do you move hydrogen around the world? And particularly Japan, and Korea, and some parts of Europe are very interested in this idea of taking and making ammonia in parts of the world that have a lot of excess energy, and then transporting the ammonia here, converting it to hydrogen locally.
And that's where we are going to start. That's going to be our first commercial application. We are really pleased to announce just recently that we have signed a joint development agreement with LOTTE Chemical, LOTTE Fine Chemical, and Sumitomo Corporation of America to do our first field-scale commercial pilot or field trial here in Korea. It's going to be at the Ilsan facility.
And that'll be at the end of 2023. And that will be taking ammonia and converting it into about 200 kilograms per day of hydrogen. We're really excited that both LOTTE and Sumitomo have chosen us as part of their very important climate technology strategies.
And then there's a similar use case around the decarbonization of a port. So similarly, you would make the ammonia somewhere else in the world, bring it into the port, convert it to hydrogen locally. And when you use that zero emissions technology to convert it into hydrogen and then use that hydrogen to power fuel cells, you have no emissions at the port associated with any of this part of the process. So again, lots of areas of the world that are very interested in this type of technology.
So I'm going to end by talking about how we think we integrate into the market. Our core technology is the catalyst and the reactor. And that's what we're going to continue to focus on. And that means that we need partners across the rest of the value chain to collaborate with.
So we'll be working with partners to help us design and build the reactor banks that will allow the module scale-up of the reactor side. So for instance, if we're bringing in a 200 kilogram per day reactor, we could put that into a bank of 5 and produce a ton a day of hydrogen from that reactor bank. We'll also be working with systems engineering and EPC partners to design and build the rest of the Balance of Plant and help us integrate into either existing facilities or into new facilities.
And the end game is that we'll have operators with a fully integrated facility that allows them to produce either hydrogen or synthetic fuels with much lower emissions, much lower cost than the current technology. And this is just the start for us. Again, we're starting with this idea of producing either hydrogen or synthetic fuels. But as I mentioned, this is a platform technology where we can look at a lot of other chemical reactions in the future.
So we'd be very interested to speak with any of you who might have some interest in this technology. And I'll be at the showcase a little bit later. Thank you very much.
[APPLAUSE]
-
Interactive transcript
[APPLAUSE]
SPEAKER: [KOREAN SPEECH]
LYNN FROSTMAN: Good afternoon. It's my pleasure to tell you a little bit more about Syzygy Plasmonics today. My name is Lynn Frostmann, and we are electrifying the chemical industry.
We basically have a way to run chemical reactions with light instead of heat, and thereby reduce both emissions and cost. And we're proud to be affiliated with MIT as one of The Engine's member companies.
So this is a pretty simplified view of the chemical industry that we're targeting. But the main take-home message is that there are several key intermediate molecules that make up a vast majority of the end use products or go into them. So if you want to have an impact on the sustainability of the chemical industry, focusing on these intermediate molecules is a great way to get the maximum amount of impact.
And the challenge in the chemical industry is that many of the reactions are powered by catalysts. And those catalysts need heat to operate. And that heat is typically generated by the combustion of fossil fuels right now.
Those combustion processes contribute about a gigaton of CO2 emissions every year right now. And this is a very difficult challenge to solve to help decarbonize the chemical industry. What we're bringing to the table is a new type of reactor. It works with LED lights instead of with heat.
And that allows us to fully electrify the chemical reaction process, and thereby reducing the emissions. This is based on two basic sets of innovations, one around the photocatalyst. It is the world's most stable and active photocatalyst. It's the result of 30 years of research at Rice University that has now been commercialized by Syzygy.
And the great thing about this-- it is a platform technology. So we can look at many different types of chemical reactions with these different catalysts. And we are starting with a couple of key ones.
One is looking at the decomposition of ammonia to give hydrogen. The other is looking at dry methane reforming, which allows you to take methane and CO2 and convert those into SYN gas, which then can be used to produce synthetic fuels and methanol. But because we have to run our reactors with light, we had to create a whole new type of chemical reactor.
So we build our reactors out of glass, and regular stainless steel, and some aluminum, and some plastics. And because we're able to use these more commodity-type of materials, it allows us to lower the cost of the chemical reactors. We don't need any hastelloy in there. We operate at much lower temperatures, much lower pressures.
So let's talk about a specific use case. As many of you may have heard, there's a lot of folks interested in hydrogen right now as one of the transition fuels. And in order to make hydrogen and transport it-- transporting is actually one of the bigger challenges.
So there's a lot of people who are looking at this idea of using ammonia as that transport carrier. How do you move hydrogen around the world? And particularly Japan, and Korea, and some parts of Europe are very interested in this idea of taking and making ammonia in parts of the world that have a lot of excess energy, and then transporting the ammonia here, converting it to hydrogen locally.
And that's where we are going to start. That's going to be our first commercial application. We are really pleased to announce just recently that we have signed a joint development agreement with LOTTE Chemical, LOTTE Fine Chemical, and Sumitomo Corporation of America to do our first field-scale commercial pilot or field trial here in Korea. It's going to be at the Ilsan facility.
And that'll be at the end of 2023. And that will be taking ammonia and converting it into about 200 kilograms per day of hydrogen. We're really excited that both LOTTE and Sumitomo have chosen us as part of their very important climate technology strategies.
And then there's a similar use case around the decarbonization of a port. So similarly, you would make the ammonia somewhere else in the world, bring it into the port, convert it to hydrogen locally. And when you use that zero emissions technology to convert it into hydrogen and then use that hydrogen to power fuel cells, you have no emissions at the port associated with any of this part of the process. So again, lots of areas of the world that are very interested in this type of technology.
So I'm going to end by talking about how we think we integrate into the market. Our core technology is the catalyst and the reactor. And that's what we're going to continue to focus on. And that means that we need partners across the rest of the value chain to collaborate with.
So we'll be working with partners to help us design and build the reactor banks that will allow the module scale-up of the reactor side. So for instance, if we're bringing in a 200 kilogram per day reactor, we could put that into a bank of 5 and produce a ton a day of hydrogen from that reactor bank. We'll also be working with systems engineering and EPC partners to design and build the rest of the Balance of Plant and help us integrate into either existing facilities or into new facilities.
And the end game is that we'll have operators with a fully integrated facility that allows them to produce either hydrogen or synthetic fuels with much lower emissions, much lower cost than the current technology. And this is just the start for us. Again, we're starting with this idea of producing either hydrogen or synthetic fuels. But as I mentioned, this is a platform technology where we can look at a lot of other chemical reactions in the future.
So we'd be very interested to speak with any of you who might have some interest in this technology. And I'll be at the showcase a little bit later. Thank you very much.
[APPLAUSE]