
11.8.22-Tokyo-Showcase-Skylla-Technologies
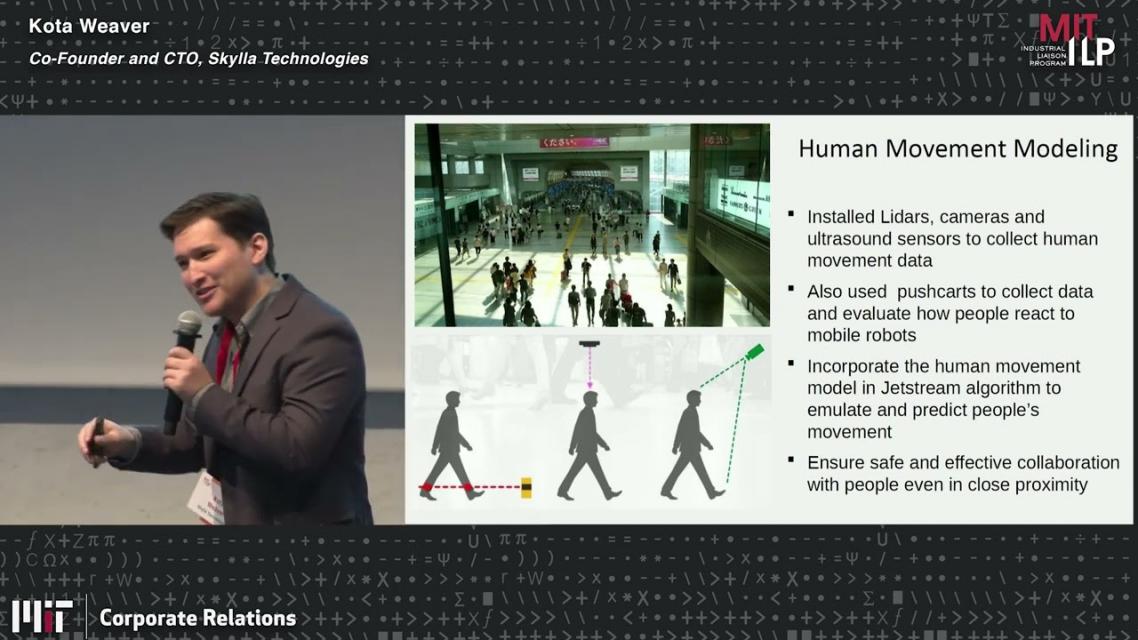
-
Interactive transcript
KOTA WEAVER: Think I need to-- yeah, I'm going to roam a little bit. Hi, thank you so much for having me here. I'm Kota Weaver here representing Skylla. I'm going to talk about mobile robotics.
And we're based in Boston area, the center of robotic innovation in the United States, as a spin-off of MIT. And here I just want to highlight on the far left here one of our founders, Harry Asada, who used to teach at Kyoto University and then Carnegie Mellon and now teaches at MIT. The inventor of direct-drive robotics is one of our founders.
So a lot of factories in Japan look like this on the left. It's because over many, many years, there's been a lot of money poured into them. And they've been making a lot of changes as their needs change. But ideally, they look like the ones on the right. And that transition is something that's really difficult.
Now, there are a lot of different things that prevent these factories from really leveraging everything that they can. And that includes things like just a lack of space. And these factories are really living places. So they change on a day to day. And that makes bringing mobile robots to make those factories look more like the one on the right very difficult.
We have a controller that solves a lot of these problems, that serves as the brain for your mobile robots. And I guess basically they provide better intelligence, agility, and accuracy. So at the heart of it all is our human-centric navigation. So I don't know if you've seen any robots in grocery stores, or I think in Japan they have them in department stores as well.
And whenever anyone is near them, or if there's any sort of obstruction, they immediately stop and they look pretty much useless. I don't really understand the full point of them. And the reason for that is because they don't understand how humans move.
So that same issue is something that you see in the factories. If, for example, something breaks down, then the entire factory floor might have to stop operation. That's because people have to go in and make those changes. And the robots and machines can't account for that.
We have gone ahead and taught robots the little interactions that allow people to avoid those kinds of collisions when we're actually operating in these same conditions. And that allows robots to be safer and more effective in these factories. I just want to also point out we have-- once you've driven around, you still have to be able to do things. So we have about a 0.3 millimeter end-point positioning accuracy.
So going back to this human-aware navigation, we've taken data using LiDAR sensors and collected terabytes of data of people just walking around, of small interactions. When you're walking down the sidewalk and someone is going the other way, when you're about 20 meters away, you do that little dance. Everyone does this, where you do that little dance, where you see them shift to the left, shift-- and you shift to the right. And that interaction allows you to communicate how to actually navigate smoothly.
We detect the same information in our robots and that allows us to better navigate through factory environments. We have IPs to protect all of this robot-to-human collaboration, robot-to-robot collaboration, human movement model, et cetera. And I want to showcase just one use case, one customer that we have here in Japan. This is DMG MORI. And they use Jetstream, our technology, to power the WH-AMR5. WH-AMR5 is a mobile manipulator that transfers work pieces and tools between different machines.
And these are being used across Japan. The reason for that is because, in these factories that are often very congested and with the declining workforce, they need a solution that can handle all of those cases. We've also been helping them release a couple of other products. We have two main products. So there's-- or a few main products, Jetstream, and then the Fleet Management Server.
And together they provide a comprehensive solution. We tend to work closely with our customers on an NRE basis, so that we can better understand your specific needs. And we want to incorporate that knowledge that we gain into our platform to make factories better globally. So just a few areas that we're currently in or that we think we're a good fit for, things like inspection, machine tending, material transfer. These are all areas that we either currently have a footprint or we think Jetstream would be a good fit for.
So we're currently looking for customers, strategic partners, to develop new mobile manipulation platforms or to retrofit existing ones for things like indoor and outdoor hybrid use cases, or clean room applications. We're also looking for a partnership for fleet management-related navigation development. We have a long history of working with companies in East Asia, specifically in Japan.
And we also have a partnership with a company that has a presence both in Japan and Korea that will serve as our main distribution and support contact. Thank you very much.
[SPEAKING JAPANESE]
-
Interactive transcript
KOTA WEAVER: Think I need to-- yeah, I'm going to roam a little bit. Hi, thank you so much for having me here. I'm Kota Weaver here representing Skylla. I'm going to talk about mobile robotics.
And we're based in Boston area, the center of robotic innovation in the United States, as a spin-off of MIT. And here I just want to highlight on the far left here one of our founders, Harry Asada, who used to teach at Kyoto University and then Carnegie Mellon and now teaches at MIT. The inventor of direct-drive robotics is one of our founders.
So a lot of factories in Japan look like this on the left. It's because over many, many years, there's been a lot of money poured into them. And they've been making a lot of changes as their needs change. But ideally, they look like the ones on the right. And that transition is something that's really difficult.
Now, there are a lot of different things that prevent these factories from really leveraging everything that they can. And that includes things like just a lack of space. And these factories are really living places. So they change on a day to day. And that makes bringing mobile robots to make those factories look more like the one on the right very difficult.
We have a controller that solves a lot of these problems, that serves as the brain for your mobile robots. And I guess basically they provide better intelligence, agility, and accuracy. So at the heart of it all is our human-centric navigation. So I don't know if you've seen any robots in grocery stores, or I think in Japan they have them in department stores as well.
And whenever anyone is near them, or if there's any sort of obstruction, they immediately stop and they look pretty much useless. I don't really understand the full point of them. And the reason for that is because they don't understand how humans move.
So that same issue is something that you see in the factories. If, for example, something breaks down, then the entire factory floor might have to stop operation. That's because people have to go in and make those changes. And the robots and machines can't account for that.
We have gone ahead and taught robots the little interactions that allow people to avoid those kinds of collisions when we're actually operating in these same conditions. And that allows robots to be safer and more effective in these factories. I just want to also point out we have-- once you've driven around, you still have to be able to do things. So we have about a 0.3 millimeter end-point positioning accuracy.
So going back to this human-aware navigation, we've taken data using LiDAR sensors and collected terabytes of data of people just walking around, of small interactions. When you're walking down the sidewalk and someone is going the other way, when you're about 20 meters away, you do that little dance. Everyone does this, where you do that little dance, where you see them shift to the left, shift-- and you shift to the right. And that interaction allows you to communicate how to actually navigate smoothly.
We detect the same information in our robots and that allows us to better navigate through factory environments. We have IPs to protect all of this robot-to-human collaboration, robot-to-robot collaboration, human movement model, et cetera. And I want to showcase just one use case, one customer that we have here in Japan. This is DMG MORI. And they use Jetstream, our technology, to power the WH-AMR5. WH-AMR5 is a mobile manipulator that transfers work pieces and tools between different machines.
And these are being used across Japan. The reason for that is because, in these factories that are often very congested and with the declining workforce, they need a solution that can handle all of those cases. We've also been helping them release a couple of other products. We have two main products. So there's-- or a few main products, Jetstream, and then the Fleet Management Server.
And together they provide a comprehensive solution. We tend to work closely with our customers on an NRE basis, so that we can better understand your specific needs. And we want to incorporate that knowledge that we gain into our platform to make factories better globally. So just a few areas that we're currently in or that we think we're a good fit for, things like inspection, machine tending, material transfer. These are all areas that we either currently have a footprint or we think Jetstream would be a good fit for.
So we're currently looking for customers, strategic partners, to develop new mobile manipulation platforms or to retrofit existing ones for things like indoor and outdoor hybrid use cases, or clean room applications. We're also looking for a partnership for fleet management-related navigation development. We have a long history of working with companies in East Asia, specifically in Japan.
And we also have a partnership with a company that has a presence both in Japan and Korea that will serve as our main distribution and support contact. Thank you very much.
[SPEAKING JAPANESE]