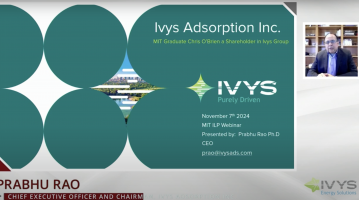
2024 Decarbonization Webinar: Startup Exchange - EvolOH

-
Interactive transcript
CATERINA MADEIRA: Next, we'll hear about EvolOH and how they are decarbonizing the chemical industry with a low cost electrochemical platform. Due to an unforeseen event, Jimmy Rojas is not able to be with us today. But I am happy to introduce you to Art Shirley, chief commercial officer at EvolOH. Art, please take it away. Thank you.
ART SHIRLEY: Certainly. And let me extend apologies from Jimmy. He had a family emergency, earlier in the week, and so was unable to do this. But very keen on the ties with MIT and so he wanted one of us to be here to be able to produce that.
Let me try to move through this, quickly, so we don't fall too far behind.
EvolOH was founded for the purpose of large-scale manufacturing of electrolyzer stacks. And so the story behind it is Jimmy did his couple degrees at MIT, went to Stanford, did a PhD with a focus on entrepreneurship. He ended up at Breakthrough Energy Ventures vetting hydrogen projects. And there were all sorts of interesting technology-- new catalysts, membranes, et cetera-- but no one focused on the manufacturing.
And the manufacturing is important because, if you can hit the actual targets for hydrogen-- I'll move my cursor over here on the left-- it would require gigawatts and gigawatts of supply to manufacture the hydrogen in demand. Probably through 2050, you're talking about thousands of gigawatts of installed capacity. Those stacks only last for so long-- 10 years, 15 years maybe. Consequently, you have to replace them.
And we did an estimate. It would require up to 150 factories each one making 15 gigawatts per year. That's a lot of capacity. It doesn't exist today. And so what we find is, in the industry, as people develop green hydrogen projects, only about 1 out of 10 is actually reaching a final investment decision. And that's because the costs are high and the availability is limited.
The costs are high because existing technologies use very expensive materials, precious metals, toxic membranes, very complex logistics. You see, for the alkaline electrolyzer, the picture in the middle, on the left, that was about 6 and 1/2 megawatts, weighs 80 tons. So it can't be moved over public roads or by any kind of public conveyance. You need special transport for it.
The PEM electrolyzers are smaller, more compact, but because of the use of precious metals, particularly iridium, which is a critical limitation, and the complex supply chains that go behind it, they tend to be very expensive. And then the OpEx is high. They often can't load-follow, so they can't be tied directly to renewables.
I know Mr Kinzer mentioned something about battery interfaces and how expensive those are. It really becomes a limitation to tie together low-cost renewable energy with high-volume electrolysis capacity.
And then the second part is that scaling these up to the gigawatts and gigawatts that are needed is not really possible with existing methods. The supply chains are broken. They tend to be made laboratory-style and very inefficient that way. The manufacturing processes, likewise, are not very scalable. And I'll show you some data on that.
And then the last part, which I think is critical, especially for anyone who's worked in the chemical process industry, they tend to have very limited warranties-- one or two years, defects in workmanship-- and no performance guarantees. So over the lifetime of the stack, the performance will degrade, efficiency will go down, more electricity will be used. And the manufacturer has no responsibility behind that. So trying to fix these problems becomes the real challenge in the green hydrogen space.
So EvolOH went after this in a number of ways. Number one is we went for economies of scale in manufacturing by using roll-to-roll processing. Think newsprint, something very high speed, where the parts are all made on a roll and then cut from that. And it's simple.
And in our process, all of the repeating components in the cells are made via roll-to-roll processing. It is very high speed, which means more can be produced in the same space. It's also a more compact way to make it.
The second part is we use a technology called anion exchange membrane electrolyzers, similar to the PEM electrolyzers I showed. The great thing about anion exchange membranes is it's possible to use only low-cost materials. And our focus on that was to be able to use domestic supply chains, so stainless steel, nickel foam, nickel catalyst, hydrocarbon membranes, all things that you can source literally anywhere around the globe. But because of the low cost, it makes it possible to scale the manufacturing.
And then we want to convert that into the lowest cost stack in the industry because we start with low-cost materials and a high speed manufacturing process. We estimate that our cost to manufacture would be 1/10 of the cost that we're seeing in forecasts for 2030. firms like BloombergNEF and the like have made estimates.
We believe we can manufacture for a fraction of that. And as I said, because it's only commodity materials, your limitations to scale are greatly removed because now these are available in large amounts. And then we believe that will deliver the lowest levelized cost of hydrogen.
What you see here are a couple of our 1 megawatt stacks that we've manufactured. We don't have the full roll-to-roll process, but we're getting there. It is load-follows and load-sheds instantaneously, so you can tie it directly to the renewables. And likewise, you've got lower engineering costs, because it's so compact, that you don't have a lot of installation costs or cost in the balance of plant that's required to make these.
One thing I'll point out is it's a very unique design. If you've seen many electrolyzers, they typically have big end plates, bolt circles, tension rods, and the like. Our stack doesn't have any of that. It's compressed uniformly by the wrap that goes over the top. And consequently, it doesn't have any issues with torque amongst the cells or having to retension the rods over time because of relaxation. That means it's much easier to maintain in the field.
And what's the outcome from that? Well, the graph, on the left, shows you that, as you drop the cost-- OK, so on the bottom axis-- from above 2 to below 2, you begin to open up a number of markets, which really can't be addressed by green hydrogen as it exists today. And that means the scale of the market increases dramatically. And as you see it scaled here, we go from a few gigawatts all the way up to 800 gigawatts. And that's in a 2030 sort of time frame. Because now you're able to compete with hydrocarbon sources of hydrogen and also produce at the scale that those hydrocarbon sources can produce.
And then that opens up all sorts of industrial hydrogen markets, as mentioned before, the ammonia space in steelmaking, et cetera. All of these now have the opportunity to be converted. Likewise, by making ammonia or by making methanol, you can get into any number of large range energy transfer or energy export projects. The scale of the projects now become bigger because that can be done.
Likewise, you're able to focus on making energy in one part of the world and moving it to another part. So in particular, when you look at places like the Middle East, North Africa, South Asia, particularly India, South America, where they have huge potential for, for example, solar irradiance, but they're so far from the main markets for electricity that they'll never be able to commoditize that and turn it into an export product. But now, by being able to make hydrogen with that electricity and then make these exportable products, you're able to recognize that.
One of the project developers that we're working with has a project in Mauritania for 35 gigawatts of electrolysis capacity, which is more than all the electrolysis capacity installed to date. So we're very excited to see these kind of big projects become possible, realizable through this technology.
In fact, we recently closed our first sale. It's 500 megawatts for a very large renewable energy producer who makes ammonia-- will make ammonia with it. And that's a binding sale contract. It's not a letter of intent. But certainly, there's money behind it.
A few last thoughts here. Our factories, because they're high speed, they have a smaller footprint, which reduces building costs, they have lower equipment costs, as well. What you see in the graph, on the left, is the factory cost per gigawatt per year of manufacturing.
You see EvolOH down below $20 million, pardon me, per gigawatt. Whereas you see some of the participants in the space, Cummins and Plug Power and the like, who are much more expensive. Typically, it's around $100 million per gigawatt. We'll bring it in at a fifth of that cost because it's very compact. And that allows you to do that kind of vertical integration, where material comes in one door and out the other door as product, very quickly.
High inventory turnover becomes an important measurement of the production cost. And that would allow us to be able to do negative cash conversion cycles in the long run. In other words, you get paid before you pay for the raw materials.
And our third party assessments of this manufacturing cost, you see in the graph here. Some of the markers are hidden. But anywhere from 100 units, so 100 electrolyzer stacks per year, to 10,000 electrolyzer stacks per year, you see a very gradual drop off in that manufacturing cost. It cost you about 2 and 1/2 times, here, what it does cost you, here, to make stacks. And that means you don't have to fully load the factory before you're able to produce at low cost.
We have a single product, this 1 megawatt stack, which we can build into larger units in shipping containers. We've proven those stack material costs exceptionally low levels. And the third party, some of you may be familiar with Strategic Analysis who did this for us.
And so what that means? When you break down the cost of the stack, we believe we can go to market $200 a kilowatt. And you see the cost of materials and manufacturing and warranty in there, which means there's plenty of room to be able to move that and manage lower cost even going forward.
I just want to say something quickly about our partners. Of course, our lead investor, the Engine Ventures, they are from the MIT community. Breakthrough Energy and SAFAR Partners, our development partners, some of whom are also investors, Nextera Energy-- the largest renewable energy developer in the Americas, perhaps one of the largest in the world. And we have some exciting projects going on with them. 3M, the guys who practically wrote the book on roll-to-roll processing, so very exciting to be doing some development with them. And then SoCalGas, who is very much focused on using their gas grid for hydrogen, moving hydrogen, and hydrogen projects and the like.
Some of the things we're doing nos-- working on large-scale commercial pilots, multi-megawatt scale pilots. We're working with a number of EPCs on the engineering and balance of plant design. And then, of course, talking to developers around the globe to be able to bring these projects forward.
And I think I brought it in under time. So, Caterina, I'll let you take over.
CATERINA MADEIRA: Thank you. Thank you very much, Art, for the presentation. We have a few questions for you, as well.
The first one is AEM membrane part of the innovation of EvolOH or AEM is purchased off-the-shelf from supplier?
ART SHIRLEY: That's a great question. We do not make the membrane. And we do not source membranes from other startups who make AEMs. And part of the reason behind that is because they're startups. They're developing a product. They typically don't have the quality procedures in place. They typically don't have the scale to manufacture that would allow us to do gigawatts per year.
I think the last count I heard of was we're working with four different multinational membrane manufacturers. Lots of people have seen interest in this place, particularly with the issues around the PFAS materials, which are used in the proton exchange membrane electrolyzers. And so, consequently, lots of large membrane manufacturers are wanting to get into this space.
We evaluate those materials. Our intention is to go to market as a membrane agnostic manufacturer, which means we can source from a number of parties and still deliver the same performance and lifetime that we will warrant for our product.
CATERINA MADEIRA: OK. Thank you. What are developers or EPCs demanding from OEMs like EvolOH? And are those demands being met?
ART SHIRLEY: So another great question. One of the things I touched on before was that, typically, for an electrolyzer manufacturer, they have a very limited warranty-- one or two years defects in workmanship, no performance guarantee, over time or even initially. And so consequently, when an EPC builds a plant, he has to wrap a warranty around the entire plant that promises the project developer, the owner, that it will use this much electricity to make this much hydrogen, it will have a certain amount of uptime, the maintenance will be at a certain cost. And the limited warranties that are typically issued in this field become very challenging.
Our focus is to issue-- we're still working on the details with an insurer, but we believe we'll be able to go to market with a lifetime warranty. Think like the warranty you get on your automobile tires of 5 to 8 years when we put our product in the market.
CATERINA MADEIRA: Thank you. A final question for you. Can you clarify why several news sites say that supply is much higher than demand?
ART SHIRLEY: Yeah. So that's a question of paper capacity versus real capacity. So after 2020, 2021, lots of companies, incumbents, startups, et cetera, announced factories that they intended to build. But frankly, because they're so expensive, most of those have not come to fruition. No one's even put a shovel in the ground. And so consequently, that capacity on paper looks quite large. But the reality is the actual manufacturing capacity is quite limited.
And I'll say this, EvolOH, we announced a 3.75 gigawatt per year factory in Lowell, Massachusetts, which we intend to start up in 2026. It appears in a lot of lists of factories. Even though we occupy the site, we have our development equipment there-- I showed you a picture before with the stacks that were at that site-- but it does not manufacture at 3.75 gigawatts per year today. So we have to be very careful and put a jaundiced eye on some of these estimates, because they take press releases and tabulate from that. And the vast majority of those plants do not exist.
CATERINA MADEIRA: Thank you very much, Art. And thank you again, [INAUDIBLE], for being with us today.
-
Interactive transcript
CATERINA MADEIRA: Next, we'll hear about EvolOH and how they are decarbonizing the chemical industry with a low cost electrochemical platform. Due to an unforeseen event, Jimmy Rojas is not able to be with us today. But I am happy to introduce you to Art Shirley, chief commercial officer at EvolOH. Art, please take it away. Thank you.
ART SHIRLEY: Certainly. And let me extend apologies from Jimmy. He had a family emergency, earlier in the week, and so was unable to do this. But very keen on the ties with MIT and so he wanted one of us to be here to be able to produce that.
Let me try to move through this, quickly, so we don't fall too far behind.
EvolOH was founded for the purpose of large-scale manufacturing of electrolyzer stacks. And so the story behind it is Jimmy did his couple degrees at MIT, went to Stanford, did a PhD with a focus on entrepreneurship. He ended up at Breakthrough Energy Ventures vetting hydrogen projects. And there were all sorts of interesting technology-- new catalysts, membranes, et cetera-- but no one focused on the manufacturing.
And the manufacturing is important because, if you can hit the actual targets for hydrogen-- I'll move my cursor over here on the left-- it would require gigawatts and gigawatts of supply to manufacture the hydrogen in demand. Probably through 2050, you're talking about thousands of gigawatts of installed capacity. Those stacks only last for so long-- 10 years, 15 years maybe. Consequently, you have to replace them.
And we did an estimate. It would require up to 150 factories each one making 15 gigawatts per year. That's a lot of capacity. It doesn't exist today. And so what we find is, in the industry, as people develop green hydrogen projects, only about 1 out of 10 is actually reaching a final investment decision. And that's because the costs are high and the availability is limited.
The costs are high because existing technologies use very expensive materials, precious metals, toxic membranes, very complex logistics. You see, for the alkaline electrolyzer, the picture in the middle, on the left, that was about 6 and 1/2 megawatts, weighs 80 tons. So it can't be moved over public roads or by any kind of public conveyance. You need special transport for it.
The PEM electrolyzers are smaller, more compact, but because of the use of precious metals, particularly iridium, which is a critical limitation, and the complex supply chains that go behind it, they tend to be very expensive. And then the OpEx is high. They often can't load-follow, so they can't be tied directly to renewables.
I know Mr Kinzer mentioned something about battery interfaces and how expensive those are. It really becomes a limitation to tie together low-cost renewable energy with high-volume electrolysis capacity.
And then the second part is that scaling these up to the gigawatts and gigawatts that are needed is not really possible with existing methods. The supply chains are broken. They tend to be made laboratory-style and very inefficient that way. The manufacturing processes, likewise, are not very scalable. And I'll show you some data on that.
And then the last part, which I think is critical, especially for anyone who's worked in the chemical process industry, they tend to have very limited warranties-- one or two years, defects in workmanship-- and no performance guarantees. So over the lifetime of the stack, the performance will degrade, efficiency will go down, more electricity will be used. And the manufacturer has no responsibility behind that. So trying to fix these problems becomes the real challenge in the green hydrogen space.
So EvolOH went after this in a number of ways. Number one is we went for economies of scale in manufacturing by using roll-to-roll processing. Think newsprint, something very high speed, where the parts are all made on a roll and then cut from that. And it's simple.
And in our process, all of the repeating components in the cells are made via roll-to-roll processing. It is very high speed, which means more can be produced in the same space. It's also a more compact way to make it.
The second part is we use a technology called anion exchange membrane electrolyzers, similar to the PEM electrolyzers I showed. The great thing about anion exchange membranes is it's possible to use only low-cost materials. And our focus on that was to be able to use domestic supply chains, so stainless steel, nickel foam, nickel catalyst, hydrocarbon membranes, all things that you can source literally anywhere around the globe. But because of the low cost, it makes it possible to scale the manufacturing.
And then we want to convert that into the lowest cost stack in the industry because we start with low-cost materials and a high speed manufacturing process. We estimate that our cost to manufacture would be 1/10 of the cost that we're seeing in forecasts for 2030. firms like BloombergNEF and the like have made estimates.
We believe we can manufacture for a fraction of that. And as I said, because it's only commodity materials, your limitations to scale are greatly removed because now these are available in large amounts. And then we believe that will deliver the lowest levelized cost of hydrogen.
What you see here are a couple of our 1 megawatt stacks that we've manufactured. We don't have the full roll-to-roll process, but we're getting there. It is load-follows and load-sheds instantaneously, so you can tie it directly to the renewables. And likewise, you've got lower engineering costs, because it's so compact, that you don't have a lot of installation costs or cost in the balance of plant that's required to make these.
One thing I'll point out is it's a very unique design. If you've seen many electrolyzers, they typically have big end plates, bolt circles, tension rods, and the like. Our stack doesn't have any of that. It's compressed uniformly by the wrap that goes over the top. And consequently, it doesn't have any issues with torque amongst the cells or having to retension the rods over time because of relaxation. That means it's much easier to maintain in the field.
And what's the outcome from that? Well, the graph, on the left, shows you that, as you drop the cost-- OK, so on the bottom axis-- from above 2 to below 2, you begin to open up a number of markets, which really can't be addressed by green hydrogen as it exists today. And that means the scale of the market increases dramatically. And as you see it scaled here, we go from a few gigawatts all the way up to 800 gigawatts. And that's in a 2030 sort of time frame. Because now you're able to compete with hydrocarbon sources of hydrogen and also produce at the scale that those hydrocarbon sources can produce.
And then that opens up all sorts of industrial hydrogen markets, as mentioned before, the ammonia space in steelmaking, et cetera. All of these now have the opportunity to be converted. Likewise, by making ammonia or by making methanol, you can get into any number of large range energy transfer or energy export projects. The scale of the projects now become bigger because that can be done.
Likewise, you're able to focus on making energy in one part of the world and moving it to another part. So in particular, when you look at places like the Middle East, North Africa, South Asia, particularly India, South America, where they have huge potential for, for example, solar irradiance, but they're so far from the main markets for electricity that they'll never be able to commoditize that and turn it into an export product. But now, by being able to make hydrogen with that electricity and then make these exportable products, you're able to recognize that.
One of the project developers that we're working with has a project in Mauritania for 35 gigawatts of electrolysis capacity, which is more than all the electrolysis capacity installed to date. So we're very excited to see these kind of big projects become possible, realizable through this technology.
In fact, we recently closed our first sale. It's 500 megawatts for a very large renewable energy producer who makes ammonia-- will make ammonia with it. And that's a binding sale contract. It's not a letter of intent. But certainly, there's money behind it.
A few last thoughts here. Our factories, because they're high speed, they have a smaller footprint, which reduces building costs, they have lower equipment costs, as well. What you see in the graph, on the left, is the factory cost per gigawatt per year of manufacturing.
You see EvolOH down below $20 million, pardon me, per gigawatt. Whereas you see some of the participants in the space, Cummins and Plug Power and the like, who are much more expensive. Typically, it's around $100 million per gigawatt. We'll bring it in at a fifth of that cost because it's very compact. And that allows you to do that kind of vertical integration, where material comes in one door and out the other door as product, very quickly.
High inventory turnover becomes an important measurement of the production cost. And that would allow us to be able to do negative cash conversion cycles in the long run. In other words, you get paid before you pay for the raw materials.
And our third party assessments of this manufacturing cost, you see in the graph here. Some of the markers are hidden. But anywhere from 100 units, so 100 electrolyzer stacks per year, to 10,000 electrolyzer stacks per year, you see a very gradual drop off in that manufacturing cost. It cost you about 2 and 1/2 times, here, what it does cost you, here, to make stacks. And that means you don't have to fully load the factory before you're able to produce at low cost.
We have a single product, this 1 megawatt stack, which we can build into larger units in shipping containers. We've proven those stack material costs exceptionally low levels. And the third party, some of you may be familiar with Strategic Analysis who did this for us.
And so what that means? When you break down the cost of the stack, we believe we can go to market $200 a kilowatt. And you see the cost of materials and manufacturing and warranty in there, which means there's plenty of room to be able to move that and manage lower cost even going forward.
I just want to say something quickly about our partners. Of course, our lead investor, the Engine Ventures, they are from the MIT community. Breakthrough Energy and SAFAR Partners, our development partners, some of whom are also investors, Nextera Energy-- the largest renewable energy developer in the Americas, perhaps one of the largest in the world. And we have some exciting projects going on with them. 3M, the guys who practically wrote the book on roll-to-roll processing, so very exciting to be doing some development with them. And then SoCalGas, who is very much focused on using their gas grid for hydrogen, moving hydrogen, and hydrogen projects and the like.
Some of the things we're doing nos-- working on large-scale commercial pilots, multi-megawatt scale pilots. We're working with a number of EPCs on the engineering and balance of plant design. And then, of course, talking to developers around the globe to be able to bring these projects forward.
And I think I brought it in under time. So, Caterina, I'll let you take over.
CATERINA MADEIRA: Thank you. Thank you very much, Art, for the presentation. We have a few questions for you, as well.
The first one is AEM membrane part of the innovation of EvolOH or AEM is purchased off-the-shelf from supplier?
ART SHIRLEY: That's a great question. We do not make the membrane. And we do not source membranes from other startups who make AEMs. And part of the reason behind that is because they're startups. They're developing a product. They typically don't have the quality procedures in place. They typically don't have the scale to manufacture that would allow us to do gigawatts per year.
I think the last count I heard of was we're working with four different multinational membrane manufacturers. Lots of people have seen interest in this place, particularly with the issues around the PFAS materials, which are used in the proton exchange membrane electrolyzers. And so, consequently, lots of large membrane manufacturers are wanting to get into this space.
We evaluate those materials. Our intention is to go to market as a membrane agnostic manufacturer, which means we can source from a number of parties and still deliver the same performance and lifetime that we will warrant for our product.
CATERINA MADEIRA: OK. Thank you. What are developers or EPCs demanding from OEMs like EvolOH? And are those demands being met?
ART SHIRLEY: So another great question. One of the things I touched on before was that, typically, for an electrolyzer manufacturer, they have a very limited warranty-- one or two years defects in workmanship, no performance guarantee, over time or even initially. And so consequently, when an EPC builds a plant, he has to wrap a warranty around the entire plant that promises the project developer, the owner, that it will use this much electricity to make this much hydrogen, it will have a certain amount of uptime, the maintenance will be at a certain cost. And the limited warranties that are typically issued in this field become very challenging.
Our focus is to issue-- we're still working on the details with an insurer, but we believe we'll be able to go to market with a lifetime warranty. Think like the warranty you get on your automobile tires of 5 to 8 years when we put our product in the market.
CATERINA MADEIRA: Thank you. A final question for you. Can you clarify why several news sites say that supply is much higher than demand?
ART SHIRLEY: Yeah. So that's a question of paper capacity versus real capacity. So after 2020, 2021, lots of companies, incumbents, startups, et cetera, announced factories that they intended to build. But frankly, because they're so expensive, most of those have not come to fruition. No one's even put a shovel in the ground. And so consequently, that capacity on paper looks quite large. But the reality is the actual manufacturing capacity is quite limited.
And I'll say this, EvolOH, we announced a 3.75 gigawatt per year factory in Lowell, Massachusetts, which we intend to start up in 2026. It appears in a lot of lists of factories. Even though we occupy the site, we have our development equipment there-- I showed you a picture before with the stacks that were at that site-- but it does not manufacture at 3.75 gigawatts per year today. So we have to be very careful and put a jaundiced eye on some of these estimates, because they take press releases and tabulate from that. And the vast majority of those plants do not exist.
CATERINA MADEIRA: Thank you very much, Art. And thank you again, [INAUDIBLE], for being with us today.