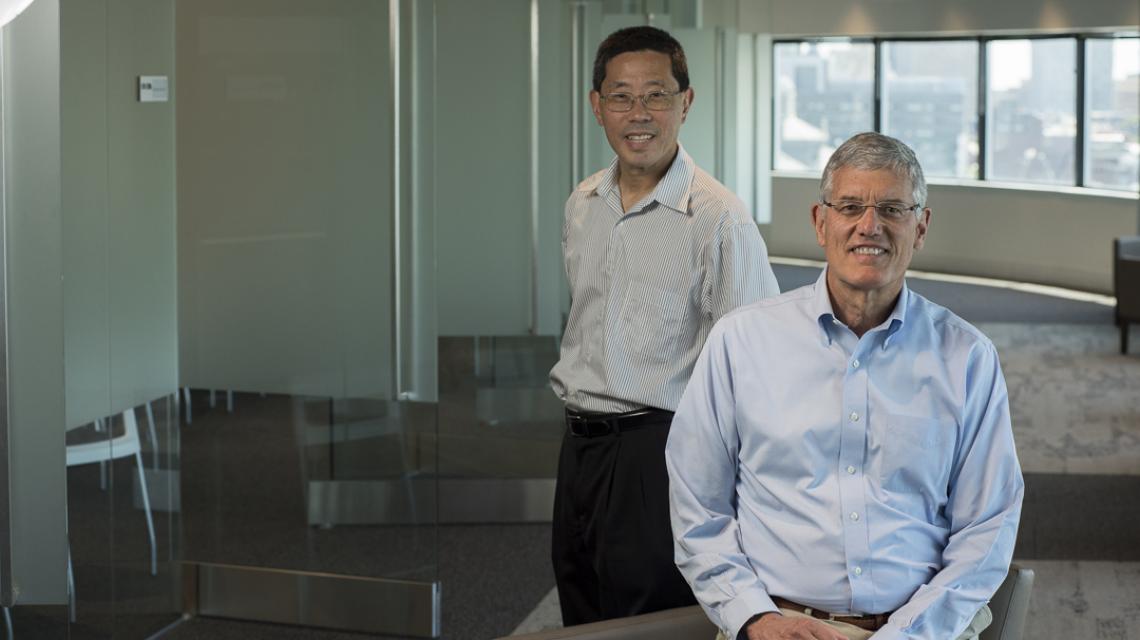
24M
Re-imagining lithium ion batteries
At 24M, Yet-Ming Chiang has revamped the way lithium ion batteries are designed and manufactured, making them a viable low-cost, highly-efficient green energy option.
For nearly 25 years, Yet-Ming Chiang has been designing and building new battery technologies in the Department of Materials Science and Engineering at MIT. Hand-in-hand with his research endeavors, he has always been active moving that science from the lab to industry having co-founded several companies, including American Superconductor Corporation, A123Systems, SpringLeaf Therapeutics, and his latest, 24M, which is in the business of designing highly-efficient, lower-cost lithium ion batteries.
Developed in the late 1980s in Japan, lithium ion batteries are today’s most advanced battery technology dominating battery applications from hand-held devices to electric vehicles, and increasingly, grid energy storage. But Dr. Chiang believes the technology is being held back due to quarter century-old methods of battery design and manufacturing that persist today.
24M’s manufacturing method strips out about 1/3 of the steps, or unit operations, of previous manufacturing methods. It also eliminates the need for any organic solvents which are used in conventional lithium ion manufacturing that have to be evaporated and re-condensed.
Chiang and colleagues formed 24M in 2010 to remedy those deficiencies. They have developed a cell design that makes much more efficient use of the materials that go into a lithium ion battery. Specifically, their designs decrease the amount of material that does not store energy by 40% or more. By maximizing the amount of active, energy storage material and decreasing all other materials, 24M reduces the bill of materials by 25-30% compared to conventional lithium ion batteries.
“24M is the culmination of a lot of things that we’ve learned both in research and through the industrialization of new battery technologies,” says Chiang. “Having earlier developed a battery technology that was a new chemistry and was put into commercialization but manufactured the conventional way, I had learned a lot about what the weaknesses of the conventional manufacturing were.”
Novel Manufacturing Method
“Our vision for the company is that the way that we manufacture lithium ion batteries will become the preferred way for making batteries around the world,” Chiang says. 24M’s manufacturing method strips out about 1/3 of the steps, or unit operations, of previous manufacturing methods. It also eliminates the need for any organic solvents which are used in conventional lithium ion manufacturing that have to be evaporated and re-condensed. “By avoiding these steps that were used earlier, we’ve also decreased the energy consumption of our manufacturing method.” Chiang estimates 24M’s battery design and manufacturing methods provide a 25% reduction in cost of goods versus conventional lithium ion batteries.
“What impresses me about what Yet has done is that he hasn’t come up with a radically new chemistry for the battery, but he has modified its design and radically changed the manufacturing process,” says Rick Feldt, 24M President. “We use a lot less stuff and it takes us half as many steps to actually produce the cell. When you have less materials, fewer steps, smaller building, fewer people, less equipment, a faster process – it all adds up to creating a lot of savings.”
Partnerships, not Plants
24M’s business model is to partner with those that want to produce their own batteries. “In a sense we are trying to democratize the production of lithium ion batteries so that any company can do it – not just a few select companies around the world,” Chiang explains. Companies can license 24M’s technology without having to invest in gigawatt hour sized plants. Companies can more accurately match supply with demand as their business grows, rather than investing significant capital for capacity in advance of demand. As an additional benefit, the licensing agreements allow 24M’s partners to modify the battery design to more specifically suit their applications.
24M sees three main applications for LI batteries today – portable devices, transportation, and energy storage for the grid or to smooth renewable energy. They are avoiding the hand-held market at this point, and targeting the large-scale applications.
Their first product, now ready for manufacturing, is a battery for grid energy storage. 24M signed its first partnership agreement with Thailand’s GPSC, part of the country’s largest oil and gas company, PTT. They are in discussions with a large industrial Japanese company now for a similar type of deal.
Some of their potential partners in this space are other countries concerned about grid energy storage solutions. They see it as a national resource, a national priority, to be in the position of producing their own batteries for energy storage. “We offer them an alternative way, a lower cost battery, a manufacturing method that we think is the future,” Chiang says, that removes reliance on other countries and companies for their battery supply.
24M sees three main applications for LI batteries today – portable devices, transportation, and energy storage for the grid or to smooth renewable energy.
24M is also very close to marketing a higher energy density lithium ion battery for transportation. “The goals for battery technology are to get the costs of batteries down and the driving range up to where it’s easy for anyone to use an electric vehicle with minimal limitations on user behavior,” Chiang says, who adds that getting the cost of a lithium ion battery pack down to about $100 per kilowatt hour is what is required. “What we are aiming to do is accelerate the adoption of electric transportation by providing the lowest cost lithium ion batteries that anyone can produce because of the greater design and efficiency of our manufacturing method.”
The company is in discussion with a number of global organizations for electric vehicle applications. “In all cases, these partners will rely on our technology and we will be the technology provider,” says Feldt. “They will build the factories, buy the equipment, and operate those factories with our help and we will share in the economics of those factories.”
Chiang emphasizes that lithium ion technology is not a single technology, though lithium is the key chemical component. “There is a lot of effort today, and we’re involved in that effort ourselves, in developing a lithium-metal electrode based rechargeable battery.” Lithium ion currently does not use lithium metal, but Chiang explains that using lithium metal as one of the battery’s electrodes would allow a 2-3-fold increase in the energy density of today’s batteries.
“There are certainly a lot of different chemistries being explored all the time,” he says. “What we are focused on is the fact that as other chemistries get developed, if the chemistries prove to be useful and successful and low cost, we will have a way of dropping them into 24M’s approach.”
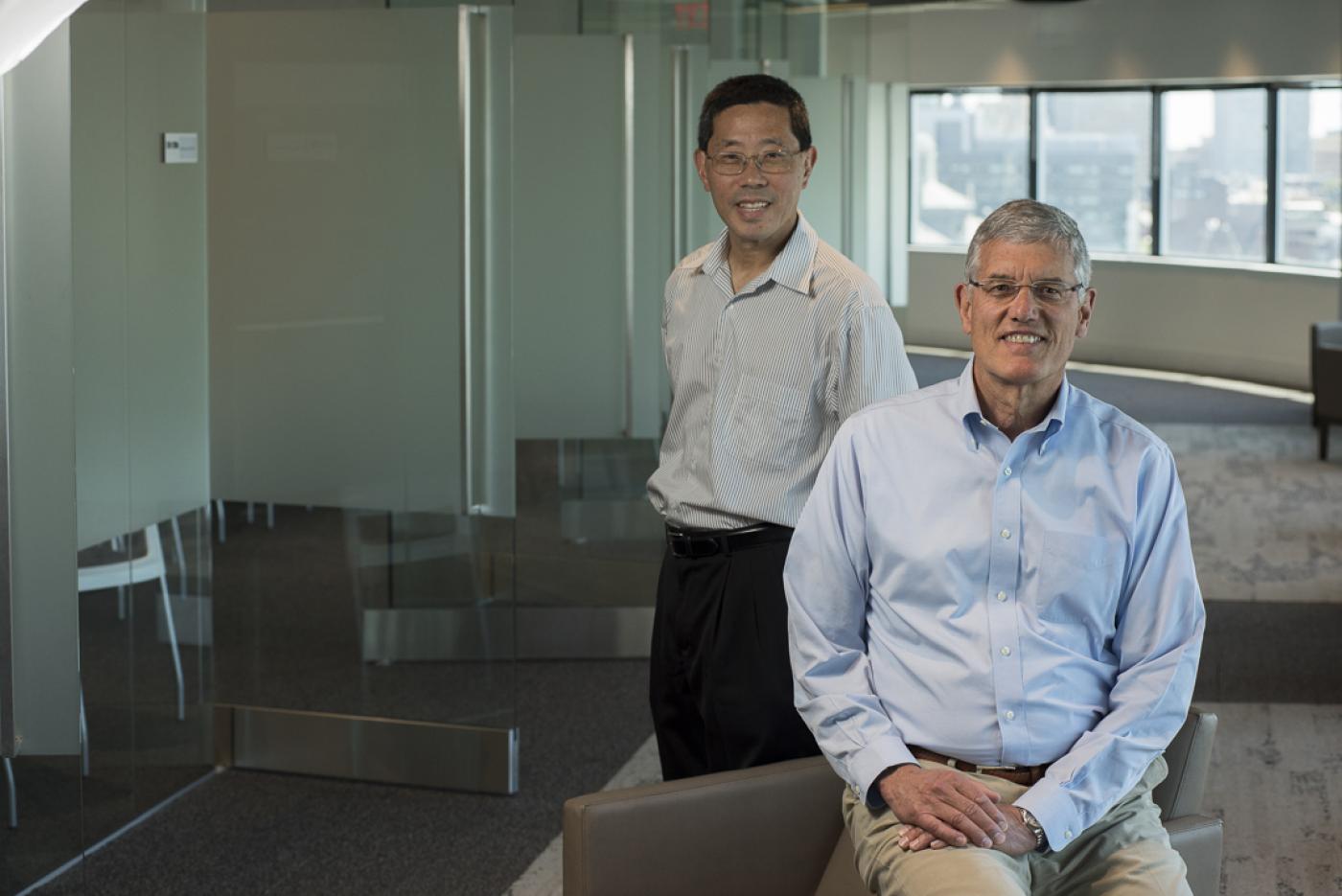