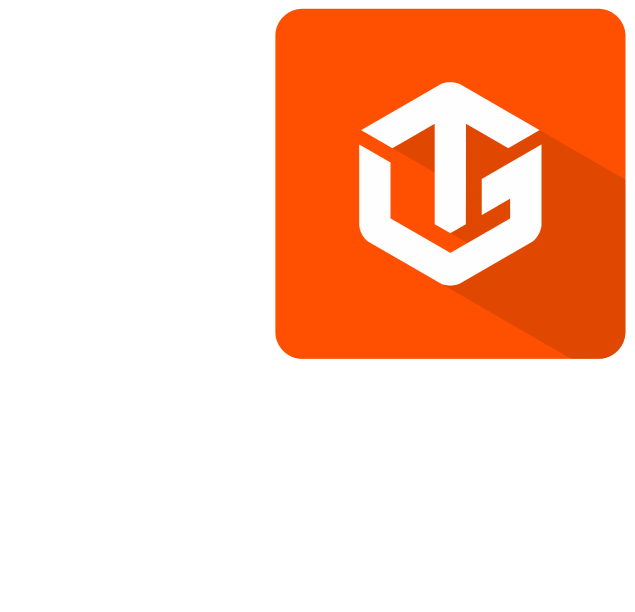
Tagup
Tagup: Industrial Equipment Meets the Cloud
Tagup’s platform tracks equipment operation and avoids unplanned downtime.
On Jon Garrity’s iPhone, Tagup is displaying a power transformer at a nearby power plant: not just photos of the transformer, but real-time data on the equipment’s operations such as the temperature and dissolved gas level of its oil. If there were any clues here of something just starting to go wrong, an expert might spot them immediately.
We help reduce unplanned downtime, which has huge costs in lost output and productivity. Monitoring data continuously coming off this equipment, an operator or third-party expert can identify an issue before it occurs.”
That’s the core point of the Tagup platform, which connects industrial equipment to cloud-based services. Tagup provides remote visibility of the equipment, along with better understanding and predictions of its performance, to operators, third-party experts and manufacturers.
“We help reduce unplanned downtime, which has huge costs in lost output and productivity,” says Garrity, co-founder and CEO of Tagup, a member of the MIT Startup Exchange 25 based in Somerville, Massachusetts. “Monitoring data continuously coming off this equipment, an operator or third-party expert can identify an issue before it occurs.”
These benefits are compounded by the ability to generate better operational models by analyzing industrial equipment at scale. “We’re collecting a much higher-resolution set of data, and we can collect it across a much larger sample size,” says Garrity. His co-founder (and fellow MIT alum) Will Vega-Brown, an expert in machine language and software, is leading the company’s efforts to exploit these analytic opportunities.
Watching from the cloud
Current monitoring systems for high-cost machinery such as gas turbines offer a glimpse of what Tagup delivers more broadly. In one example, General Electric sells a gas turbine with an accompanying remote monitoring solution. A GE network operating center can watch the performance of more than 1,700 gas turbines around the world, with a team that identifies any problems starting to crop up and then helps operators deal with the problem proactively.
“Our platform enables that type of service for any equipment type,” Garrity says. “If you’re operating, say, a power transformer, instead of relying on once- or twice-a-year oil sampling, you can have third-party experts monitoring the data continuously, with computer analytics, to help you cut downtime.”
As industrial machines join the Internet of Things, Tagup aims to fill a huge and growing gap. “Currently there is no way to simply remotely monitor a diverse number of equipment types and share that data with third parties,” Garrity says.
One challenge is that different pieces of equipment work on different data and communication protocols, some of which have been around since the 1960s, he explains. Tagup translates the data from these older protocols into a modern web protocol, so that developers can build the tools and the analytics required to enhance, modernize and optimize equipment operation in the field.
Sometimes this installed equipment can make its operating data accessible remotely, sometimes not. “If not, we connect the equipment directly with an off-the-shelf industrial cellular gateway—basically a rugged cell phone,” he says.
Making the connection is typically straightforward—getting information about the equipment and the data it provides to provide a “digital twin” and then going onsite to hook up the gateway, which can take as little as 15 minutes. “The rest we do remotely,” Garrity says. “Data coming off that equipment is sent securely to our cloud, where we parse, store and analyze that data, and then make it accessible to users through our application. Our customers are looking for turnkey value, and that’s what we provide.”
Proactive help for steady production
Among early Tagup installations are reverse osmosis systems that deliver purified water. These systems use membranes, whose performance degrades over time. “With Tagup, you can remotely monitor how efficient your membranes are, and you can see when they need to be replaced,” Garrity says.
One customer, a value-added reseller for reverse osmosis systems, can see in real-time the health of all equipment that they have installed, and prioritize its maintenance operations. Instead of visiting each plant every three months, the reseller can focus on locations where maintenance issues are coming up. And it can do so across various types of reverse-osmosis facilities. “They’re using one software interface to check on the health of all the equipment they’ve installed and serviced to date,” Garrity says.
Additionally, the Tagup platform can offer major payoffs for equipment manufacturers. “They can know exactly who the end customer is, exactly where the product is and exactly how well that equipment is performing,” he says. “There’s also a new sales and service opportunity presented to them, moving from a pure equipment sale to a higher-margin service business.”
Moreover, the value of equipment monitoring increases with scale, which allows the generation of better models for predicting equipment health and performance. “The results from our machine language analytics are not yet established, but we’re optimistic about their capabilities,” Garrity says.
For example, in a power transformer, how does the oil’s temperature correlate with a given maintenance concern? “We can build models that take into account, say, 30 of these variables, looking across thousands of transformers, to help identify problems that wouldn’t be picked up by existing models,” he says. “The more data we integrate, the better analytical models we can make, and we can just push these models to the cloud.”
“Given the size of the industrial Internet of Things, the market for these applications is enormous,” Garrity points out. “For instance, sales of new power transformers make up about a $6.5 billion annual market, on top of a large installed base. Analyzing the operational data via our platform and helping customers cut their unplanned downtime creates real value.”
