
10.25.23-Digital-MontBlancAI
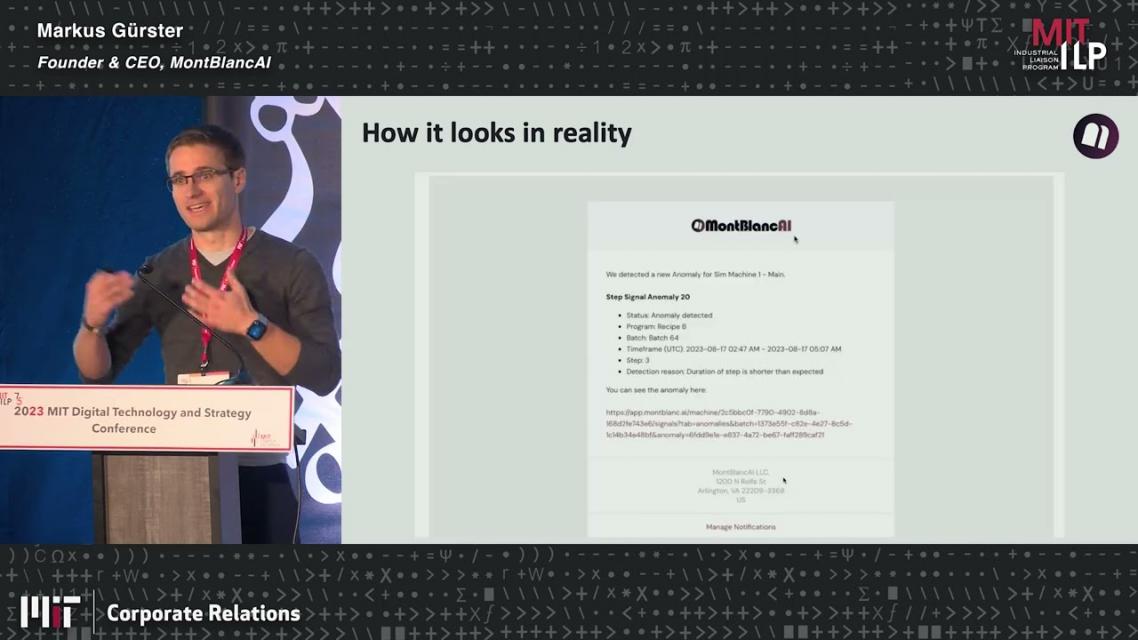
-
Video details
AI-driven dispatching and routing for last-mile deliveries
-
Interactive transcript
MARKUS GURSTER: Hello, everyone. A real pleasure to be here today also hello to everyone on the live stream. My name is Markus. I'm founder and CEO of MontBlancAI. And what we are doing, we're basically the digital powerhouse for smart factories. So simply put, we bring AI into the manufacturing industry.
The problem that we encountered, if you look across different manufacturing sites, is that the equipment that is running there is only an uptime of 60% to 70%. And there's obviously, productivity losses and waste resulting out of this. Of course, the manufacturers are completely aware. They know that they have to improve their uptime to increase productivity.
But if you look at the current systems that they have in place, they're completely inadequate to actually help that. And one of the main reasons is that hundreds of petabytes of data is just not leveraged. It's either on a PLCs or it's somewhere in some databases or data lakes just lying around.
So our solution, basically, turns that data into insights. So it gives recommendations and trends like, will your productivity increase, the energy consumption reduced, we detected a spike in some of your pumps, so you maybe want to change the pump in the future.
The core of all of this is our anomaly-detection algorithms. And it leverages a variety of different AI techniques. So on one side, we have the real-time data coming in, and then we put really a lot of effort into pre-processing because you have to have clean data, and you only can compare apples to apples and oranges to oranges.
Then the next step is to go into an unsupervised learning step. So no need for long labeling. This is all offloaded towards the back of the process. Once the models then are learned accordingly, we start anomaly detection. And at that stage, we push out all the anomalies issues that we are detecting to the floor plan on the operating site.
Once those anomalies are detected, the user gets an interface that they can really interact with. So it's a generative AI-based, and they describe the problem they can do a deep route cause analysis. And then in the end, that feeds back into our learning process. So this is where the labeling part comes in.
So how does this look in real? Well, this is an example of an email that's being sent out. So if you click on this, you get a very carefully designed dashboard that gives you insights into what you actually-- what's happening, why they detected something, what is the underlying signals?
You can compare it to history. You can see our predictions. You can add additional signals, tax, you can do basically a variety of different ways that help you to get to the root cause. Now, once you find the root cause, you can add conversational mode. You can add comments.
Well, this is because the valve didn't switch, for example. Once you submit that comment, it's being analyzed by our generative AI engine, put into context, and say, well, this is really an anomaly and being feed back into our anomaly detection process.
The other really cool thing is, that once we detect an anomaly on one machine, it goes across the whole factory. So it might be impacting one parts of the line one parts of the equipment, which can have downstream or upstream impact. And this is really where we can trace it end to end across the whole factory.
Now, to go a little bit of a case study here. So we are working with a medium- to large-sized German dairy factory that's producing over 2,000,000 liters of milk per day. They have a specific membrane filtration equipment. And they basically asked us, are the resources can to be saved, and how do they continuously validate their CIPs? So basically, a cleaning process of that machine.
The way we implemented it, we just connected to all the data sources, streaming all of the data in, putting it through our platform, and the outcome is that well over 1,000 cleaning cycles are now by validated. And they really boost the confidence of their quality assurance, as well as that's also something they can put in front of the auditors and say, yes, our cleaning cycles are completely accurate.
Now, what we're looking here for, for today, is basically additional pilot partners. We are generally industry agnostic with a focus, though, on food and beverage, oil and gas, CPG manufacturing, and semiconductor manufacturing. The ideal partner has a factory that is open for innovation and pilots, has already some sort of semi-automated automated equipment and lines running, but somehow suffers a little bit from silos of disconnected systems. So in other words, a bit of a data mess and run their equipment in multiple shifts, ideally, 24 for 7.
Now, we don't have any restrictions to any region or so. We're a global company, and we'd love to explore some global opportunities. So if that roughly sounds like something you're interested or if you know somebody who is interested in that, come stop by our booth or scan the QR code online and connect with me. And we can continue the conversation.
-
Video details
AI-driven dispatching and routing for last-mile deliveries
-
Interactive transcript
MARKUS GURSTER: Hello, everyone. A real pleasure to be here today also hello to everyone on the live stream. My name is Markus. I'm founder and CEO of MontBlancAI. And what we are doing, we're basically the digital powerhouse for smart factories. So simply put, we bring AI into the manufacturing industry.
The problem that we encountered, if you look across different manufacturing sites, is that the equipment that is running there is only an uptime of 60% to 70%. And there's obviously, productivity losses and waste resulting out of this. Of course, the manufacturers are completely aware. They know that they have to improve their uptime to increase productivity.
But if you look at the current systems that they have in place, they're completely inadequate to actually help that. And one of the main reasons is that hundreds of petabytes of data is just not leveraged. It's either on a PLCs or it's somewhere in some databases or data lakes just lying around.
So our solution, basically, turns that data into insights. So it gives recommendations and trends like, will your productivity increase, the energy consumption reduced, we detected a spike in some of your pumps, so you maybe want to change the pump in the future.
The core of all of this is our anomaly-detection algorithms. And it leverages a variety of different AI techniques. So on one side, we have the real-time data coming in, and then we put really a lot of effort into pre-processing because you have to have clean data, and you only can compare apples to apples and oranges to oranges.
Then the next step is to go into an unsupervised learning step. So no need for long labeling. This is all offloaded towards the back of the process. Once the models then are learned accordingly, we start anomaly detection. And at that stage, we push out all the anomalies issues that we are detecting to the floor plan on the operating site.
Once those anomalies are detected, the user gets an interface that they can really interact with. So it's a generative AI-based, and they describe the problem they can do a deep route cause analysis. And then in the end, that feeds back into our learning process. So this is where the labeling part comes in.
So how does this look in real? Well, this is an example of an email that's being sent out. So if you click on this, you get a very carefully designed dashboard that gives you insights into what you actually-- what's happening, why they detected something, what is the underlying signals?
You can compare it to history. You can see our predictions. You can add additional signals, tax, you can do basically a variety of different ways that help you to get to the root cause. Now, once you find the root cause, you can add conversational mode. You can add comments.
Well, this is because the valve didn't switch, for example. Once you submit that comment, it's being analyzed by our generative AI engine, put into context, and say, well, this is really an anomaly and being feed back into our anomaly detection process.
The other really cool thing is, that once we detect an anomaly on one machine, it goes across the whole factory. So it might be impacting one parts of the line one parts of the equipment, which can have downstream or upstream impact. And this is really where we can trace it end to end across the whole factory.
Now, to go a little bit of a case study here. So we are working with a medium- to large-sized German dairy factory that's producing over 2,000,000 liters of milk per day. They have a specific membrane filtration equipment. And they basically asked us, are the resources can to be saved, and how do they continuously validate their CIPs? So basically, a cleaning process of that machine.
The way we implemented it, we just connected to all the data sources, streaming all of the data in, putting it through our platform, and the outcome is that well over 1,000 cleaning cycles are now by validated. And they really boost the confidence of their quality assurance, as well as that's also something they can put in front of the auditors and say, yes, our cleaning cycles are completely accurate.
Now, what we're looking here for, for today, is basically additional pilot partners. We are generally industry agnostic with a focus, though, on food and beverage, oil and gas, CPG manufacturing, and semiconductor manufacturing. The ideal partner has a factory that is open for innovation and pilots, has already some sort of semi-automated automated equipment and lines running, but somehow suffers a little bit from silos of disconnected systems. So in other words, a bit of a data mess and run their equipment in multiple shifts, ideally, 24 for 7.
Now, we don't have any restrictions to any region or so. We're a global company, and we'd love to explore some global opportunities. So if that roughly sounds like something you're interested or if you know somebody who is interested in that, come stop by our booth or scan the QR code online and connect with me. And we can continue the conversation.