
4.28.23-Korea-CONTINUUS-Pharmaceuticals
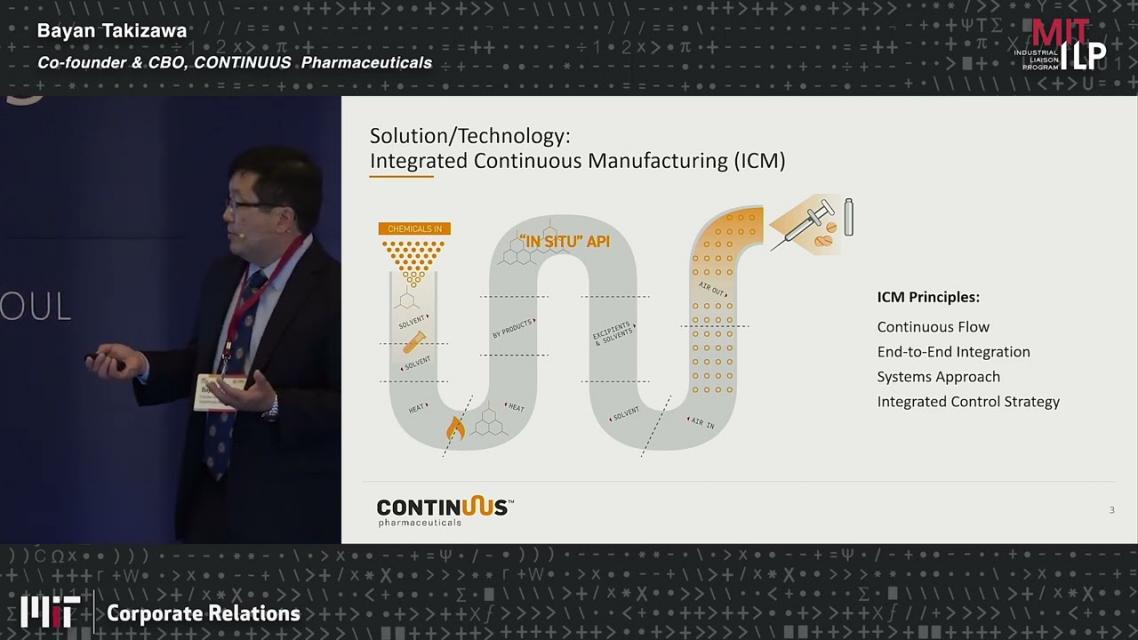
-
Interactive transcript
BAYAN TAKIZAWA: OK, good morning and thank you, organizers, for this opportunity to talk here today. My name is Bayan Takizawa and I am the co-founder and chief business officer at Continuus Pharmaceuticals. I am also an alumnus of the MIT LGO program. I'm very excited to tell you more about our company and our plans to disrupt the pharmaceutical manufacturing industry.
So what is wrong with the current manufacturing paradigm? Well, with batch manufacturing, large volumes or batches of intermediate products are produced at a single time. These intermediates are stored, tested, and then transported to the next unit operation. These steps take time, cost money, and we believe add little to no value.
In addition, the entire manufacturing process is really divided into two sections. You have your upstream chemistry and workup steps to produce the API or active pharmaceutical ingredient. And you have your downstream drug formulation, putting that API into the final dosage form that the patient takes, for example, tablets. And these activities are often done by different companies operating on different continents. And the entire process is very inefficient, resulting in over $50 billion lost every year.
More importantly, this process is not very robust and often leads to quality infractions and resulting critical drug shortages. We have a solution called Integrated Continuous Manufacturing or ICM. This innovative platform technology was initially developed at the Novartis MIT Center for Continuous Manufacturing, a $65 million joint research endeavor.
A highlight of this project is that we were able to take a 200-day batch process and cut it down to just two days. That is not incremental improvement. That is revolutionary change. Imagine now you put raw materials in one end and you get finished drug product out the other end.
No more stops and starts or isolation of intermediates, as I showed you in the previous slide. And these are just some important ICM principles that we can discuss later. So it's important to note that a lot of pharma companies are engaging in continuous manufacturing. But most are operating over here.
For example, using a single continuous unit operation where everything else is operated in batch. And so while the risk is low, the reward is also limited. And this is where we are with ICM.
A few important enablers, first, there's the implementation of novel proprietary technologies that enable fully continuous operations. Most other companies are utilizing old batch technology, but using them in a semi-continuous fashion. Then there's the end-to-end integration that I just spoke about, integrating your upstream and downstream processes into a single seamless process.
Most pharma companies are just not built that way. They have their silos, which are impossible to avoid. And then there is the versatility and flexibility of our unit operations, to be easily reconfigured in a plug-and-play fashion so as to produce different compounds. And this is some work that we did for a contract manufacturing organization on a highly potent compound that is used in the intensive care setting.
Some highlights of advantages that we were able to confer, reducing the number of unit operations from 14 to 10, eliminating operator exposure of this dangerous compound, improving the yield from 33% to 94%, and also reducing the residence time. And we estimate that we can reduce the cost of goods sold by approximately 50%, 56%, excuse me. Equally important is the ability to also reduce the environmental impact of manufacturing of this drug.
So we're in talks with several companies in Asia, including Korea. And when we think of Korea, we think of a very educated and technical workforce, high quality, and advanced manufacturing. And so we think it makes sense to leverage a technology like ICM. And here are some other reasons, lower costs, and environmentally friendly processes, safer operations for your workers, decreasing your reliance on foreign manufacturers, that is, securing a more robust supply of higher quality products while creating manufacturing jobs at home.
And then there's the improvement of innovation of new medicines. So by coupling advanced manufacturing and new drug discovery, you can develop new, better drugs and faster. Think of Taiwan's innovative semiconductor industry and how that blossomed once manufacturing was outsourced to that country.
So we're interested in talking with companies that are looking to build out advanced manufacturing facilities, companies that have vision for their pipeline. Although ICM could benefit the production of individual drugs, we really see this as a paradigm shift. Also, government agencies who might be interested in leveraging ICM strategically, for example, eliminating shortages that I mentioned earlier.
But more importantly, I'm very interested in hearing your thoughts on how we can add value to your company. So on behalf of our team back home, thank you very much, and I look forward to talking with you later today.
-
Interactive transcript
BAYAN TAKIZAWA: OK, good morning and thank you, organizers, for this opportunity to talk here today. My name is Bayan Takizawa and I am the co-founder and chief business officer at Continuus Pharmaceuticals. I am also an alumnus of the MIT LGO program. I'm very excited to tell you more about our company and our plans to disrupt the pharmaceutical manufacturing industry.
So what is wrong with the current manufacturing paradigm? Well, with batch manufacturing, large volumes or batches of intermediate products are produced at a single time. These intermediates are stored, tested, and then transported to the next unit operation. These steps take time, cost money, and we believe add little to no value.
In addition, the entire manufacturing process is really divided into two sections. You have your upstream chemistry and workup steps to produce the API or active pharmaceutical ingredient. And you have your downstream drug formulation, putting that API into the final dosage form that the patient takes, for example, tablets. And these activities are often done by different companies operating on different continents. And the entire process is very inefficient, resulting in over $50 billion lost every year.
More importantly, this process is not very robust and often leads to quality infractions and resulting critical drug shortages. We have a solution called Integrated Continuous Manufacturing or ICM. This innovative platform technology was initially developed at the Novartis MIT Center for Continuous Manufacturing, a $65 million joint research endeavor.
A highlight of this project is that we were able to take a 200-day batch process and cut it down to just two days. That is not incremental improvement. That is revolutionary change. Imagine now you put raw materials in one end and you get finished drug product out the other end.
No more stops and starts or isolation of intermediates, as I showed you in the previous slide. And these are just some important ICM principles that we can discuss later. So it's important to note that a lot of pharma companies are engaging in continuous manufacturing. But most are operating over here.
For example, using a single continuous unit operation where everything else is operated in batch. And so while the risk is low, the reward is also limited. And this is where we are with ICM.
A few important enablers, first, there's the implementation of novel proprietary technologies that enable fully continuous operations. Most other companies are utilizing old batch technology, but using them in a semi-continuous fashion. Then there's the end-to-end integration that I just spoke about, integrating your upstream and downstream processes into a single seamless process.
Most pharma companies are just not built that way. They have their silos, which are impossible to avoid. And then there is the versatility and flexibility of our unit operations, to be easily reconfigured in a plug-and-play fashion so as to produce different compounds. And this is some work that we did for a contract manufacturing organization on a highly potent compound that is used in the intensive care setting.
Some highlights of advantages that we were able to confer, reducing the number of unit operations from 14 to 10, eliminating operator exposure of this dangerous compound, improving the yield from 33% to 94%, and also reducing the residence time. And we estimate that we can reduce the cost of goods sold by approximately 50%, 56%, excuse me. Equally important is the ability to also reduce the environmental impact of manufacturing of this drug.
So we're in talks with several companies in Asia, including Korea. And when we think of Korea, we think of a very educated and technical workforce, high quality, and advanced manufacturing. And so we think it makes sense to leverage a technology like ICM. And here are some other reasons, lower costs, and environmentally friendly processes, safer operations for your workers, decreasing your reliance on foreign manufacturers, that is, securing a more robust supply of higher quality products while creating manufacturing jobs at home.
And then there's the improvement of innovation of new medicines. So by coupling advanced manufacturing and new drug discovery, you can develop new, better drugs and faster. Think of Taiwan's innovative semiconductor industry and how that blossomed once manufacturing was outsourced to that country.
So we're interested in talking with companies that are looking to build out advanced manufacturing facilities, companies that have vision for their pipeline. Although ICM could benefit the production of individual drugs, we really see this as a paradigm shift. Also, government agencies who might be interested in leveraging ICM strategically, for example, eliminating shortages that I mentioned earlier.
But more importantly, I'm very interested in hearing your thoughts on how we can add value to your company. So on behalf of our team back home, thank you very much, and I look forward to talking with you later today.