6.15.23-STEX-CA-Eion
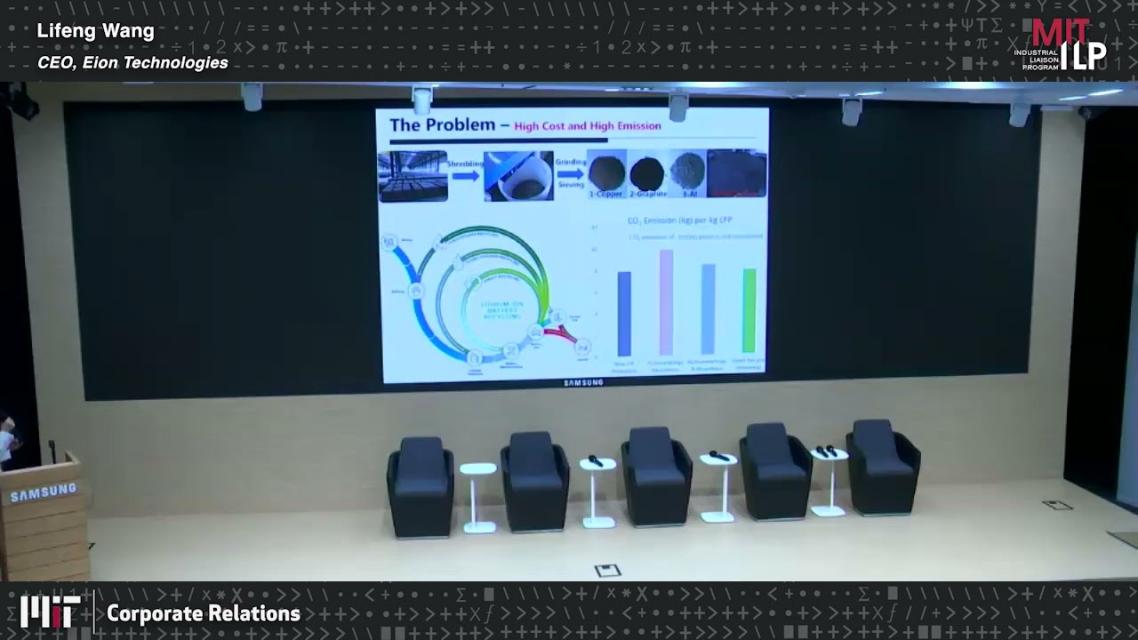
-
Interactive transcript
SPEAKER: And so last but not least for this group of startups, this is EION Technologies, and it's a new way to repair and recycle with a positive impact on the environment.
LIFENG WANG: Good morning, everybody. My name is Lifeng Wang. I'm the co-founder and CEO of EION Technologies. At EION we have developed a disruptive technology to recycle lithium iron phosphate cathode material from spent batteries, and I co-founded the company with two MIT alumni. Professor Ju Li is a professor at MIT currently of material science, and Professor Sa Li, who was an associate professor at Tongji University, and she studied at MIT for a year under Professor Ju Li.
The problem we're trying to solve is, we all know there's a lot of battery needed in today's world, and it's growing exponentially. And as we heard from Dr. Martin Scott that even for AI computing there is-- the electricity need is unsustainable and you need solar and wind power and you need energy storage system, which is mainly LFP batteries. So there will be stampede of a spent battery coming off the usage, and all of them, 100%, must be recycled because there is no other way to process the waste.
So the existing methods were recycled battery capsule material. Right now are three methods. They are parallel metallurgical method and hydro metallurgical, and there is emitting, which is the one form of direct recycling. All of them, as you can see from the chart, all of them consumes a lot of energy. They are very high cost and generate very high emission.
And the reason that they generate a lot of emission and uses a lot of energy is the spent material is only 20% to 30% of it failed. Not 100% of it. But the current method of recycling, basically recycle 100% of it, which is a deep form of recycle. So our solution to the problem that we have invented this technology that we can do targeted repair of the test of the material that we only repair the damaged part of the material instead of recycle 100% of it.
And we call it light recycling and we are able to generate very high performance, even from spent material, damaged material, but the result, the new material that we generated, it's very high performance. It's at par with the commercial grade. And we are able to cut the cost by 70% and reduce the CO2 emission by 90% and shorten the processing time by 70% as well. So it's a very fast and efficient way of recycling battery cathode material.
Here's our product. As you can see from the chart, the energy density is on par with the commercial grade lithium iron phosphate material, and actually through the technology we are able to extend the cycle life and also it's faster charging capability as well. The use case. Once we recycle this spent material, we create a new material. We sell it right back to the battery manufacturers that they can use to manufacture a new battery.
And we have tested our product with four different battery manufacturers, including one of the major automaker, GE. They own Volvo. And they have several battery manufacturing plants as well. We are going into a limited scale mass production in the second half of this year, and we are aiming to produce at least 1,000 tons over the next year, and then increase the capacity to large scale to produce a hundred tons per day of this new fresh LFP cathode material in 2024.
So we will be able to supply customers such as GE 500 times at least this year and then 10,000 times next year. And unit price. If you don't know the unit price per ton, the current market price is about $15,000 US per ton is cathode material, which is the most expensive part of the battery. The partnership that we are looking for we are building our first factory, the large scale one, and we are going to build more factories around the world wherever there is adequate amount of spent battery to be recycled.
So we look for the partnership wherever that there is enough battery and then the kind of partner that have access to source material, which is use the battery of factory scrap from battery manufacturing process. And all they have access to our potential customers, such as battery manufacturing companies like LG, XK, or the Panasonic. And here's my contact information if you are interested. Thank you very much.
SPEAKER: Thank you.
-
Interactive transcript
SPEAKER: And so last but not least for this group of startups, this is EION Technologies, and it's a new way to repair and recycle with a positive impact on the environment.
LIFENG WANG: Good morning, everybody. My name is Lifeng Wang. I'm the co-founder and CEO of EION Technologies. At EION we have developed a disruptive technology to recycle lithium iron phosphate cathode material from spent batteries, and I co-founded the company with two MIT alumni. Professor Ju Li is a professor at MIT currently of material science, and Professor Sa Li, who was an associate professor at Tongji University, and she studied at MIT for a year under Professor Ju Li.
The problem we're trying to solve is, we all know there's a lot of battery needed in today's world, and it's growing exponentially. And as we heard from Dr. Martin Scott that even for AI computing there is-- the electricity need is unsustainable and you need solar and wind power and you need energy storage system, which is mainly LFP batteries. So there will be stampede of a spent battery coming off the usage, and all of them, 100%, must be recycled because there is no other way to process the waste.
So the existing methods were recycled battery capsule material. Right now are three methods. They are parallel metallurgical method and hydro metallurgical, and there is emitting, which is the one form of direct recycling. All of them, as you can see from the chart, all of them consumes a lot of energy. They are very high cost and generate very high emission.
And the reason that they generate a lot of emission and uses a lot of energy is the spent material is only 20% to 30% of it failed. Not 100% of it. But the current method of recycling, basically recycle 100% of it, which is a deep form of recycle. So our solution to the problem that we have invented this technology that we can do targeted repair of the test of the material that we only repair the damaged part of the material instead of recycle 100% of it.
And we call it light recycling and we are able to generate very high performance, even from spent material, damaged material, but the result, the new material that we generated, it's very high performance. It's at par with the commercial grade. And we are able to cut the cost by 70% and reduce the CO2 emission by 90% and shorten the processing time by 70% as well. So it's a very fast and efficient way of recycling battery cathode material.
Here's our product. As you can see from the chart, the energy density is on par with the commercial grade lithium iron phosphate material, and actually through the technology we are able to extend the cycle life and also it's faster charging capability as well. The use case. Once we recycle this spent material, we create a new material. We sell it right back to the battery manufacturers that they can use to manufacture a new battery.
And we have tested our product with four different battery manufacturers, including one of the major automaker, GE. They own Volvo. And they have several battery manufacturing plants as well. We are going into a limited scale mass production in the second half of this year, and we are aiming to produce at least 1,000 tons over the next year, and then increase the capacity to large scale to produce a hundred tons per day of this new fresh LFP cathode material in 2024.
So we will be able to supply customers such as GE 500 times at least this year and then 10,000 times next year. And unit price. If you don't know the unit price per ton, the current market price is about $15,000 US per ton is cathode material, which is the most expensive part of the battery. The partnership that we are looking for we are building our first factory, the large scale one, and we are going to build more factories around the world wherever there is adequate amount of spent battery to be recycled.
So we look for the partnership wherever that there is enough battery and then the kind of partner that have access to source material, which is use the battery of factory scrap from battery manufacturing process. And all they have access to our potential customers, such as battery manufacturing companies like LG, XK, or the Panasonic. And here's my contact information if you are interested. Thank you very much.
SPEAKER: Thank you.