
6.22.22-Showcase-Nth Cycle
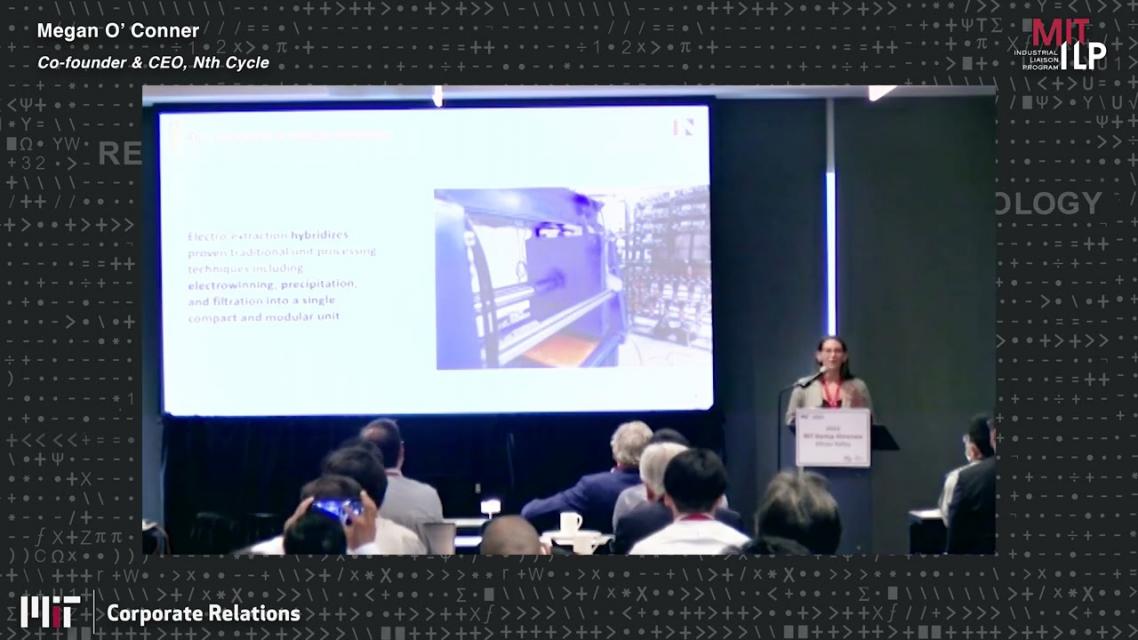
-
Video details
Creating a sustainable supply of critical minerals
-
Interactive transcript
MEGAN O'CONNER: All right. Hello, everyone. My name is Megan O'Conner. I am the CEO and one of the co-founders of Nth Cycle. We were also co-founded by MIT professor Desiree Plata.
We have developed a new technology to refine the critical minerals that we need for the energy transition. As I'm sure most of you here in the room are aware, we're facing an impending shortage of all of the critical minerals that we need to truly transition away from fossil. The other major issue we have with these critical minerals is where they are sourced from around the world.
If we take a look at this map and focus in on North America, we have a particularly large pain point in terms of how resistant-- or, sorry, reliant we are on overseas supply chains. So even if we mine the materials here in North America, 9 out of 10 times we have to ship it over to Asia to be refined into the finished or semi-finished products that we're used to seeing, like a battery or a cathode. If you follow line number two, we then buy that material back and ship it back for a second time to use here in our products.
Once we're finished with these products at their end of life as consumers, it has to be shipped back a third time, if you follow the third line back, to be landfilled or recycled in some capacity. So we're losing this valuable material three different times across its lifecycle. And so it's time that we figure out a way to refine all of these different sources of materials that we eventually have here, to keep them here in our supply chain to truly reach that circular economy that we're all looking for.
So Nth Cycle has developed that technology. Again, we can refine the different materials, both from primary ore and end-of-life scrap material, including lithium-ion batteries, a cleaner, more profitable way to do this. So we've developed a system that can be deployed on site, truly eliminating the need to transport all of these hazardous materials, again, across the world multiple times. We can easily scale our system up or down with our modular design, making it accessible for us to process all of these various sources that I mentioned before, including raw ores; the tailings, so the waste from these mine sites; and end-of-life scrap. And we can do all of this while reducing both the cost and the greenhouse gas emissions by 75% compared to traditional mining and refining technologies today.
So this technology is called electroextraction. Instead of using harsh chemicals, or solvents, or high temperatures and pressures, which are traditionally done in refining today, all we use is electricity, which can come from 100% renewable energy. So we've combined three separate unit processes that are found in refining today into one unit to truly optimize the way that we pull these different metals out of our products.
So you can think of our system at a very high level like a Brita water filter, the Brita water filter that you have home in your fridge, I would guess. So we take batteries or primary ore, and we dissolve it in a water-based solution. And we pour it through what looks like a Brita filter with a carbon filter in there.
And so when you pour your drinking water in, that Brita filter pulls out all of the metals in one stage. We have taken that same idea of using a carbon-based filter, but we've applied an electrical current across that filter. So it selectively removes one metal at a time. So you can imagine in our system, as you can see on the screen here, we have different filters stacked in series, each with a different electrical current pushed across it. So we can pull out these different materials one at a time.
So if we take a look at where Nth Cycle fits into this value chain, we'll take a look at lithium-ion battery recycling, as this-- I know this is a really big area for a lot of folks in the room today. So in lithium-ion battery recycling, we do not collect the batteries. We do not shred them down. We take it once it's become this black mass material, which is a mixture of the cathode and the anode. So we partner with folks who are doing the collection logistics and shredding.
So we take that black mass material, which is a 20% grade metal content. We turn it into a 90% metal content precursor material, which, again, significantly reduces the amount of material you have to transport to the final finishing step to become a battery. Because this is a very high-grade intermediate product, we can actually skip over the smelting step in the overall refining process. By skipping this step alone, we can save 75% of the greenhouse gas emissions of the entire process. And finally, when it reaches that final finishing step to become that next battery cathode material, we can help reduce the internal operating costs by 70% to 80%, again, because this is a much higher grade feedstock going into this final finishing step than what they would see traditionally.
So again, the products that we produce today from lithium-ion batteries from this waste black mass feedstock is a high-purity graphite material that we are currently testing in new anodes. We produce a cobalt nickel hydroxide powder, which can go into the finishing step for batteries. We produce a manganese dioxide powder and a lithium brine equivalent.
We are also working with partners-- corporate partners today to produce a direct NMC material that can go right back into cathode manufacturing, as well as the very high-purity nickel, cobalt, and manganese oxide powders. So for all of you in the room today for our various customers, we can help you improve efficiencies by refining on-site with you. We can improve your operations and reduce your internal operating costs by 70% to 80%, and help you produce the most cost-competitive and green product on the market today.
So if you're interested in working with us, we do have capacity left for two pilot opportunities this year. So you can see our process here on the right-hand side of the screen. So if you're interested, please come find me at my booth afterwards. And I look forward to speaking with you soon. Thank you.
-
Video details
Creating a sustainable supply of critical minerals
-
Interactive transcript
MEGAN O'CONNER: All right. Hello, everyone. My name is Megan O'Conner. I am the CEO and one of the co-founders of Nth Cycle. We were also co-founded by MIT professor Desiree Plata.
We have developed a new technology to refine the critical minerals that we need for the energy transition. As I'm sure most of you here in the room are aware, we're facing an impending shortage of all of the critical minerals that we need to truly transition away from fossil. The other major issue we have with these critical minerals is where they are sourced from around the world.
If we take a look at this map and focus in on North America, we have a particularly large pain point in terms of how resistant-- or, sorry, reliant we are on overseas supply chains. So even if we mine the materials here in North America, 9 out of 10 times we have to ship it over to Asia to be refined into the finished or semi-finished products that we're used to seeing, like a battery or a cathode. If you follow line number two, we then buy that material back and ship it back for a second time to use here in our products.
Once we're finished with these products at their end of life as consumers, it has to be shipped back a third time, if you follow the third line back, to be landfilled or recycled in some capacity. So we're losing this valuable material three different times across its lifecycle. And so it's time that we figure out a way to refine all of these different sources of materials that we eventually have here, to keep them here in our supply chain to truly reach that circular economy that we're all looking for.
So Nth Cycle has developed that technology. Again, we can refine the different materials, both from primary ore and end-of-life scrap material, including lithium-ion batteries, a cleaner, more profitable way to do this. So we've developed a system that can be deployed on site, truly eliminating the need to transport all of these hazardous materials, again, across the world multiple times. We can easily scale our system up or down with our modular design, making it accessible for us to process all of these various sources that I mentioned before, including raw ores; the tailings, so the waste from these mine sites; and end-of-life scrap. And we can do all of this while reducing both the cost and the greenhouse gas emissions by 75% compared to traditional mining and refining technologies today.
So this technology is called electroextraction. Instead of using harsh chemicals, or solvents, or high temperatures and pressures, which are traditionally done in refining today, all we use is electricity, which can come from 100% renewable energy. So we've combined three separate unit processes that are found in refining today into one unit to truly optimize the way that we pull these different metals out of our products.
So you can think of our system at a very high level like a Brita water filter, the Brita water filter that you have home in your fridge, I would guess. So we take batteries or primary ore, and we dissolve it in a water-based solution. And we pour it through what looks like a Brita filter with a carbon filter in there.
And so when you pour your drinking water in, that Brita filter pulls out all of the metals in one stage. We have taken that same idea of using a carbon-based filter, but we've applied an electrical current across that filter. So it selectively removes one metal at a time. So you can imagine in our system, as you can see on the screen here, we have different filters stacked in series, each with a different electrical current pushed across it. So we can pull out these different materials one at a time.
So if we take a look at where Nth Cycle fits into this value chain, we'll take a look at lithium-ion battery recycling, as this-- I know this is a really big area for a lot of folks in the room today. So in lithium-ion battery recycling, we do not collect the batteries. We do not shred them down. We take it once it's become this black mass material, which is a mixture of the cathode and the anode. So we partner with folks who are doing the collection logistics and shredding.
So we take that black mass material, which is a 20% grade metal content. We turn it into a 90% metal content precursor material, which, again, significantly reduces the amount of material you have to transport to the final finishing step to become a battery. Because this is a very high-grade intermediate product, we can actually skip over the smelting step in the overall refining process. By skipping this step alone, we can save 75% of the greenhouse gas emissions of the entire process. And finally, when it reaches that final finishing step to become that next battery cathode material, we can help reduce the internal operating costs by 70% to 80%, again, because this is a much higher grade feedstock going into this final finishing step than what they would see traditionally.
So again, the products that we produce today from lithium-ion batteries from this waste black mass feedstock is a high-purity graphite material that we are currently testing in new anodes. We produce a cobalt nickel hydroxide powder, which can go into the finishing step for batteries. We produce a manganese dioxide powder and a lithium brine equivalent.
We are also working with partners-- corporate partners today to produce a direct NMC material that can go right back into cathode manufacturing, as well as the very high-purity nickel, cobalt, and manganese oxide powders. So for all of you in the room today for our various customers, we can help you improve efficiencies by refining on-site with you. We can improve your operations and reduce your internal operating costs by 70% to 80%, and help you produce the most cost-competitive and green product on the market today.
So if you're interested in working with us, we do have capacity left for two pilot opportunities this year. So you can see our process here on the right-hand side of the screen. So if you're interested, please come find me at my booth afterwards. And I look forward to speaking with you soon. Thank you.