
9.26.23-Sustainability-Foundation-Alloy
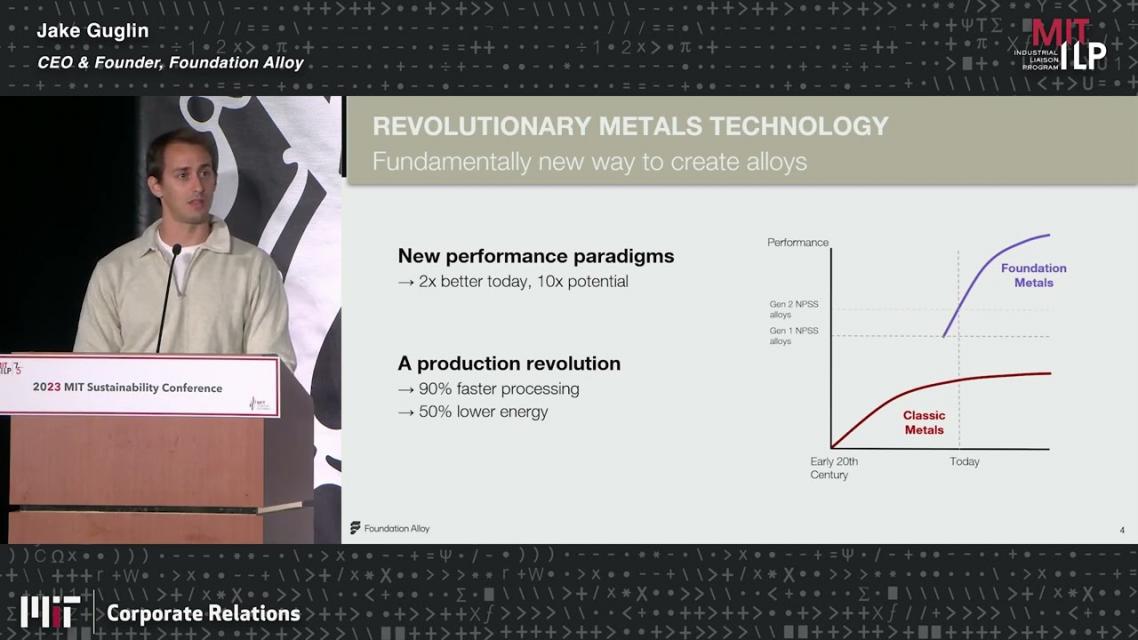
-
Video details
Engineering the Most Advanced Alloys in the World. Better Materials, Better Products, Bigger Impact
-
Interactive transcript
JAKE GUGLIN: Hi, everybody. My name is Jake Guglin. I am the co-founder and CEO of Foundation Alloy. And we are using some of the most advanced material science in the world to overhaul the $2.8 trillion metal products sector.
So to give you some context, at nearly $3 trillion, the metal products sector is larger than the US transportation, oil and gas, power generation, and aerospace and defense industries. And that's because all of these industries and more are built on metals.
They really are the foundation of modern society. And yet current technology is starting to plateau. And what this means is that performance improvements are getting increasingly more incremental, more costly, and more time-consuming, and at the same time supply chains that are already stretched are breaking, because they really aren't made to support the rate of engineering that we're seeing today as industries writ large are overhauling to address climate change.
And so there are a lot of companies that are approaching this from the advanced manufacturing side. But our contention is that the best and perhaps the only way to return to an era of step change improvements, so not 10% better products but 2x, 3x, 5x better products, is to change the inputs themselves. And that's exactly what we're doing.
We are bringing to market a fundamentally new way to create metals that allows us to drive performance up while reducing processing time, processing energy, and cost. Our first product is a good example of this. It's a refractory alloy that was designed for use in demanding applications in extreme environments like high temperature and highly corrosive places.
And it is two times harder than the state of the art, and 10x faster in terms of processing while using 50% less energy in the production of parts. And so that makes it actually both the hardest and most cost-effective metal of its time. Sorry, of its kind, ever. And we're just scratching the surface.
Because this is a new technology, we'll be able to climb these performance curves for decades to come. And as we introduce new metals with similar improvements into different slices of the overall industry, we consider ourselves to be laying a new foundation where that will help enhance products that already exist, and something that new industries can be built on.
We're able to do this because of layers of innovation that represent the first major alternative to classical metallurgy in history. And it started at the labs at MIT a couple of decades ago, where we built technology that allows us to more precisely control the position of atoms, both in part production processes and in the final microstructure of metals.
This is enabled by a unique manufacturing process that also uses off-the-shelf equipment, but in a novel way, which means that we have the ability to scale this to thousands of kilograms per week, pretty direct line of sight. And when you put those two things together, it represents a high-throughput alloy creation platform that we can then plug into the existing powder metallurgy industry, giving us volume flexibility, geometric flexibility with things like 3D printing, while also improving what is the key buying metric of performance over cost by up to 50x.
I'd like to take you through a quick case study. NASA came to the labs at MIT looking for material for advanced space applications like nuclear thermal propulsion. And so we started with a refractory alloy to get that performance, but then drove it to 2 to 3 times harder than it was previously. And we also made it 3D printable, with higher quality than what's possible with other refractory alloys and less energy and time.
We at Foundation Alloy then scaled up the manufacturing of this 100x in the last eight months or so, and have actually begun making parts out of it, both through powder metallurgy and 3D printing, meaning that within the next year or so we'll be able to start putting parts on NASA's doorstep, as well as our other customers. And our solution, when considering the performance improvements and the supply chain improvements, is a 20x increase in performance over acquisition cost compared to the current state of the art.
Where we are today, we have our first paying customers. And we are actively working with others to develop applications where better materials, faster lead times, quicker engineering cycles can help enable better performance in their products. So if you're looking for improvement in refractory alloys, better operating temperatures, overall durability gains, or efficiency gains, please come talk to me. We'd love to see if we can be the foundation for your next innovation as well. Thank you.
-
Video details
Engineering the Most Advanced Alloys in the World. Better Materials, Better Products, Bigger Impact
-
Interactive transcript
JAKE GUGLIN: Hi, everybody. My name is Jake Guglin. I am the co-founder and CEO of Foundation Alloy. And we are using some of the most advanced material science in the world to overhaul the $2.8 trillion metal products sector.
So to give you some context, at nearly $3 trillion, the metal products sector is larger than the US transportation, oil and gas, power generation, and aerospace and defense industries. And that's because all of these industries and more are built on metals.
They really are the foundation of modern society. And yet current technology is starting to plateau. And what this means is that performance improvements are getting increasingly more incremental, more costly, and more time-consuming, and at the same time supply chains that are already stretched are breaking, because they really aren't made to support the rate of engineering that we're seeing today as industries writ large are overhauling to address climate change.
And so there are a lot of companies that are approaching this from the advanced manufacturing side. But our contention is that the best and perhaps the only way to return to an era of step change improvements, so not 10% better products but 2x, 3x, 5x better products, is to change the inputs themselves. And that's exactly what we're doing.
We are bringing to market a fundamentally new way to create metals that allows us to drive performance up while reducing processing time, processing energy, and cost. Our first product is a good example of this. It's a refractory alloy that was designed for use in demanding applications in extreme environments like high temperature and highly corrosive places.
And it is two times harder than the state of the art, and 10x faster in terms of processing while using 50% less energy in the production of parts. And so that makes it actually both the hardest and most cost-effective metal of its time. Sorry, of its kind, ever. And we're just scratching the surface.
Because this is a new technology, we'll be able to climb these performance curves for decades to come. And as we introduce new metals with similar improvements into different slices of the overall industry, we consider ourselves to be laying a new foundation where that will help enhance products that already exist, and something that new industries can be built on.
We're able to do this because of layers of innovation that represent the first major alternative to classical metallurgy in history. And it started at the labs at MIT a couple of decades ago, where we built technology that allows us to more precisely control the position of atoms, both in part production processes and in the final microstructure of metals.
This is enabled by a unique manufacturing process that also uses off-the-shelf equipment, but in a novel way, which means that we have the ability to scale this to thousands of kilograms per week, pretty direct line of sight. And when you put those two things together, it represents a high-throughput alloy creation platform that we can then plug into the existing powder metallurgy industry, giving us volume flexibility, geometric flexibility with things like 3D printing, while also improving what is the key buying metric of performance over cost by up to 50x.
I'd like to take you through a quick case study. NASA came to the labs at MIT looking for material for advanced space applications like nuclear thermal propulsion. And so we started with a refractory alloy to get that performance, but then drove it to 2 to 3 times harder than it was previously. And we also made it 3D printable, with higher quality than what's possible with other refractory alloys and less energy and time.
We at Foundation Alloy then scaled up the manufacturing of this 100x in the last eight months or so, and have actually begun making parts out of it, both through powder metallurgy and 3D printing, meaning that within the next year or so we'll be able to start putting parts on NASA's doorstep, as well as our other customers. And our solution, when considering the performance improvements and the supply chain improvements, is a 20x increase in performance over acquisition cost compared to the current state of the art.
Where we are today, we have our first paying customers. And we are actively working with others to develop applications where better materials, faster lead times, quicker engineering cycles can help enable better performance in their products. So if you're looking for improvement in refractory alloys, better operating temperatures, overall durability gains, or efficiency gains, please come talk to me. We'd love to see if we can be the foundation for your next innovation as well. Thank you.