Continuus Pharmaceuticals
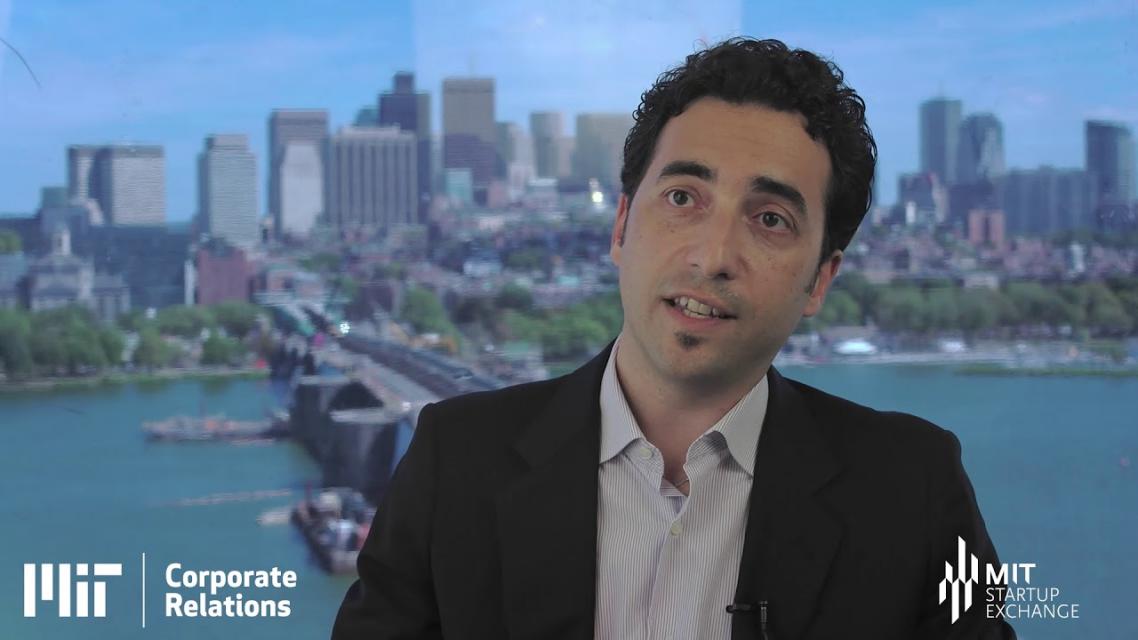
-
Video details
Salvatore Mascia
Founder and CEO
CONTINUUS Pharmaceuticals
-
Interactive transcript
SALVATORE MASCIA: My name is Salvatore Mascia. I'm the founder and CEO of CONTINUUS Pharmaceutical. CONTINUUS Pharmaceutical is an MIT spin out company which has developed a novel continuous manufacturing process for producing pharmaceuticals on-demand much more efficiently, quicker, at significant reduced cost and with better quality.
The technology was initially developed at MIT within the Novartis MIT-Center for Continuous Manufacturing, a tenure collaboration between Novartis at MIT whose objective was to completely redesign the way we develop and manufacture pharmaceuticals. I was involved within the Novartis-MIT Center since its inception working directly with Professor Bernhardt Trout, who is the current director, and we developed a new set of process technology that runs continuously, which can now be applied to many pharmaceuticals.
Our first implementation at MIT in the research lab was extremely successful. That made me convinced that there was a huge opportunity for a novel startup company now to get out there, license the technology from MIT, and make sure that this is available to the broader pharmaceutical industry.
The way pharmaceuticals are produced right now is through a sequence of very long and segmented steps done in batches. You can run a reaction in a large vessel, your structured product, needs to be tested, validated, and so forth. Then you move to the next step for another intermediate. At the end in your chemical facility, you produce an active pharmaceutical ingredient.
This then needs to be transported to other facilities when it gets formulated, made into tablets, coated, and finally sold. This is a very long and expensive step.
So what we did is basically to redesign another process technology that allows the integration of all these steps in one single solution. For us, continuous manufacturing means starting from raw material going down to a final pharmaceutical product in one single solution, in one process, if you like, which is fully automated which runs 24 hour a day, 365 days per year, under fully automated control. Through this continuous operation in automation, the drug can be produced much faster and thus significantly reduce cost.
This can be used for any drug which is basically chemically made. We are applying this to any type of small molecule pharmaceutical. The reason why this has never been really done before, because there has not been financial pressure within the pharmaceutical company to make this change. Pharmaceuticals commonly has always been running very high margins of blockbuster drug and cost of manufacturing has been always a small portion.
Things have been changed in the last decade with the incoming product of generic pharmaceuticals, looking more like a specialized type of therapy which require manufacturing processes which need to produce this pharmaceutical much more effectively. So the entire business model of the pharmaceutical industry has changed, and now those costs of manufacturing, those efficiencies, have become critical. That's why there is a huge trend in our investing in novel manufacturing of pharmaceuticals.
An example how much faster we can produce a drug through this technique rather in batch is very clear through the work that we did at MIT on the [INAUDIBLE] fumarate, a drug for high blood pressure. This product has a lead time like 200 days from beginning to the end. We were able to cut down this in two days, 48 hours. Think about this, a reduction in process lead time of more than 90%. This is a real transformation for the pharmaceutical industry. It will enable it to produce pharmaceuticals on-demand.
Basically, our projections show that the reduction in cost of goods, cost of manufacturing, could be like greater than 5-%. So if you think about that for pharmaceutical industry we're reaching a trillion dollars in total revenue with $200 billion in cost of manufacturing, we could save potentially $100 billion a year in cost of manufacturing to the entire industry by applying this technique.
[MUSIC PLAYING]
-
Video details
Salvatore Mascia
Founder and CEO
CONTINUUS Pharmaceuticals
-
Interactive transcript
SALVATORE MASCIA: My name is Salvatore Mascia. I'm the founder and CEO of CONTINUUS Pharmaceutical. CONTINUUS Pharmaceutical is an MIT spin out company which has developed a novel continuous manufacturing process for producing pharmaceuticals on-demand much more efficiently, quicker, at significant reduced cost and with better quality.
The technology was initially developed at MIT within the Novartis MIT-Center for Continuous Manufacturing, a tenure collaboration between Novartis at MIT whose objective was to completely redesign the way we develop and manufacture pharmaceuticals. I was involved within the Novartis-MIT Center since its inception working directly with Professor Bernhardt Trout, who is the current director, and we developed a new set of process technology that runs continuously, which can now be applied to many pharmaceuticals.
Our first implementation at MIT in the research lab was extremely successful. That made me convinced that there was a huge opportunity for a novel startup company now to get out there, license the technology from MIT, and make sure that this is available to the broader pharmaceutical industry.
The way pharmaceuticals are produced right now is through a sequence of very long and segmented steps done in batches. You can run a reaction in a large vessel, your structured product, needs to be tested, validated, and so forth. Then you move to the next step for another intermediate. At the end in your chemical facility, you produce an active pharmaceutical ingredient.
This then needs to be transported to other facilities when it gets formulated, made into tablets, coated, and finally sold. This is a very long and expensive step.
So what we did is basically to redesign another process technology that allows the integration of all these steps in one single solution. For us, continuous manufacturing means starting from raw material going down to a final pharmaceutical product in one single solution, in one process, if you like, which is fully automated which runs 24 hour a day, 365 days per year, under fully automated control. Through this continuous operation in automation, the drug can be produced much faster and thus significantly reduce cost.
This can be used for any drug which is basically chemically made. We are applying this to any type of small molecule pharmaceutical. The reason why this has never been really done before, because there has not been financial pressure within the pharmaceutical company to make this change. Pharmaceuticals commonly has always been running very high margins of blockbuster drug and cost of manufacturing has been always a small portion.
Things have been changed in the last decade with the incoming product of generic pharmaceuticals, looking more like a specialized type of therapy which require manufacturing processes which need to produce this pharmaceutical much more effectively. So the entire business model of the pharmaceutical industry has changed, and now those costs of manufacturing, those efficiencies, have become critical. That's why there is a huge trend in our investing in novel manufacturing of pharmaceuticals.
An example how much faster we can produce a drug through this technique rather in batch is very clear through the work that we did at MIT on the [INAUDIBLE] fumarate, a drug for high blood pressure. This product has a lead time like 200 days from beginning to the end. We were able to cut down this in two days, 48 hours. Think about this, a reduction in process lead time of more than 90%. This is a real transformation for the pharmaceutical industry. It will enable it to produce pharmaceuticals on-demand.
Basically, our projections show that the reduction in cost of goods, cost of manufacturing, could be like greater than 5-%. So if you think about that for pharmaceutical industry we're reaching a trillion dollars in total revenue with $200 billion in cost of manufacturing, we could save potentially $100 billion a year in cost of manufacturing to the entire industry by applying this technique.
[MUSIC PLAYING]
-
Video details
Salvatore Mascia
Founder and CEO
CONTINUUS Pharmaceuticals
-
Interactive transcript
SALVATORE MASCIA: The key thing is that there is a huge disconnect between the evolution of medicine and the capability of this pharmaceutical company to produce those medications. The clear example right here in Massachusetts, Massachusetts excels in the development of new therapeutics to cure many difficult diseases. More than, I think, 1,200 drugs are developed here in Massachusetts.
But the majority of these drugs are manufactured outside of the state. Most of the API, 85% of the Actual Pharmaceutical Ingredient, are coming from abroad. 45% of final dosage form are coming from abroad. There is a huge opportunity to actually change this paradigm and manufacturer those pharmaceuticals right here in the States. That's what really, again, motivates us every day to bring this business forward, to basically eliminate this gap and link the excellence in developing new therapeutics; also, in the excellence in manufacturing these new therapeutics.
As we move toward personalized medicine, a breakthrough therapy [INAUDIBLE], the FDA is continually challenging us in developing more agile and flexible manufacturing techniques, because current manufacturing assets are not feasible for this. That's where our continuous manufacturing technology will be an enabler to produce this pharmaceutical. And that's why, for us, it's so important to make this technology accessible and really revitalize the pharmaceutical manufacturing in the US and reverse all these offshoring trends which are currently taking place in the United States.
So there is an initial investment to be made because, as I was mentioning previously, the process is based on novel technology, so those novel processes don't exist right now in the market. The pharmaceutical industry, in order to keep themselves with these novel units, they will need to invest into this knowledge process. Well, we provide initially, we do a design of how this process will work on this drug for a fee, for a cost. And then in the next step, we will develop a pilot process for the pharmaceutical client that then can pay us for the transfer of this technology to the manufacturing facilities.
Obviously, we are focusing on the pharmaceuticals because there where the inefficient in manufacturing is very clear, and I can expand this a little bit later why this is important. But yes, this can be applied to chemical industry, and actually are in contact with a few of these a chemical companies who are interested to synthesizing intermediate Active Pharmaceutical Ingredient with novel technique. Could be applied to nutricutical, which is an industry which basically is less regulated than the pharmaceutical, so you can see a less barrier of entry, for instance, if you want to apply this further. So we are also looking into this opportunity. But our main core in businesses is pharmaceutical.
Include biologic as well, but our company and our technique has been developed specifically for small molecules. With that being said, we have been contacted already by some biologic company to apply some of these novel techniques to the biologic. For instance, our continuous filtration system, which can easily be applied to a certain biologic product. So there is certainly some feed through what we're doing on the small molecule into the biologic world.
We are actually in direct contact with the FDA. As I mentioned before, I'm on the steering committee of a team organizing the first international continuous manufacturing symposium here at MIT. In 2014, we actually invited Janet Woodcock, who is one of the directors at the FDA for the Center of Drug Evaluation Research. She's again, as I said before, in full support of implementation of continuous manufacturing.
And one of the comments that struck me during the conference from her was that she mentioned that the major hurdle is the concern from the pharmaceutical companies that the regulatory agency will back those processes rather than the regulatory itself. That's why I made several comments before that I think that the issue of the regulatory agency is more like a perceived risk rather than a real risk, because there is a huge emphasis from them to see this technology implemented.
[MUSIC PLAYING]
-
Video details
Salvatore Mascia
Founder and CEO
CONTINUUS Pharmaceuticals
-
Interactive transcript
SALVATORE MASCIA: There are a few things we're working on which I'm very excited about, always keeping in mind the potential this technology has to deliver medication to patient much weaker in a significant reduced cost.
One of the things that I'm really trying to make it happen is to create a center of excellence in manufacturing here in Massachusetts by basically combining research and implementation of these new processes to the pharmaceutical industry. We have done some analysis. By applying this technology to the most prescribed generic drug here in the state of Massachusetts, we could save $45 million a year in the state of Massachusetts just on Medicaid by using this novel technique. That's something very exciting, and I'm trying to push this forward.
The second point is trying to use this technology to produce pharmaceuticals for third world country, HIV medication. So basically developing and deploying those manufacturing processes in countries like Africa where we can produce pharmaceuticals at low cost and make it more affordable for many patient that actually need this.
The type of company that we would like to collaborate and work on as we move forward, I would to describe, at least right now, with these two major categories. Obviously, a large pharmaceutical company and generic company, and those because these companies have different reason to apply continuous manufacturing. Generic company is most because of their low margin. Most of their costs, 50% of their costs, versus sales is actually cost of manufacturing. So for them, it's a huge incentive to cut down the cost of this pharmaceutical in this very competitive market.
For the large pharmaceutical company, obviously the margins are larger versus the generic industry, but there are other aspects that come into play. So speed to market, flexibility, being able to dial up, dial down your capacity of production for a specific pharmaceutical to respond easily and faster to market change. And obviously, making sure that those pharmaceuticals always has a very high quality. So each company looking at the application of this technology with the different interests, and those are the companies that we would like to plug in at this stage.
Again, I would say there are three main challenges in order to make this technology applicable and commercially viable. As I mentioned, the biggest one is this industry inertia to make this change toward a novel manufacturing technique. Second one, as I mentioned, is the regulatory aspect, which as I described before is more, in my mind, of a perceived risk than actually a real risk, and the company really should try now to look forward and implement those processes rather than being concerned about the regulatory aspect.
And the third, obviously, the technology as will needs to mature. So we have a pilot process that we developed at MIT that we run for 10 days under steady state. Now the key, we need to make more robust and brought to the next level such that they can implement commercially. That's most of the work that we are doing now in our facility here in [INAUDIBLE].
So CONTINUUS Pharmaceutical has been founded two years ago, as I mentioned, as a spin out to license the technology from MIT. In these last three years, obviously, we started as most entrepreneurs do some family and friend's funds, and then we moved to angel financing. So with a couple of rounds, a seed round through convertible node with angels, we raised roughly $400,000 in seed money would help us to move on with the license with MIT and start talking with potential clients.
We also realized that as we move forward, we have to build partnership, and mainly partnership on the equipment manufacturing space, because this technology is new, so need the equipment manufacturing aspect to take this to the next level. But this is on the control and automation space, because the important part of the continuous manufacturing is to have full automation and control. So we build partnership with IMA, Industria Macchine Automatiche, one of the largest equipment manufacturing for pharmaceutical, and with Emerson through a local business partner here, New England Controls, to use their control system for our continuous manufacturing plant.
So this now creates the full picture for us to be able now to work with the pharmaceutical companies and start to develop continuous manufacturing processes for them. Thanks to the support from IMA, we actually avoid to do a series of investment through an institutional venture capital firm. Actually, IMA invested themselves $2 million in our company.
And so this really helped us to move on, setting up our lab, our operation [INAUDIBLE], and being active on the work that we are doing. In the last two years right now, we have raised more than $2.5 million between angels, strategic partnership, and grants. We have received the SBIR NSF phase 1 grant, which we have already effectively executed, and now submitted our phase 2 application.
And what we're working right now, it's really market validation. This July, we have closed our first contract which, I think, is a very important validation with a large multinational pharmaceutical company. And we have several other deals now with the large engineering company which are actively negotiating. That's what we're going to focus in the next year, to close this deal and take CONTINUUS to the next inflection point.
[MUSIC PLAYING]
-
Video details
Salvatore Mascia
Founder and CEO
CONTINUUS Pharmaceuticals
-
Interactive transcript
SALVATORE MASCIA: The area of the MIT ecosystem, obviously, is very unique, especially when you talk about pharmaceuticals. This is becoming the center of the world, really, for developing new drug, and now we want to make sure that this also becomes the center of the world for manufacturing this new pharmaceutical, to have a novel, cutting edge manufacturing technique.
The connection with the MIT for us has been vital. Starting, obviously, with the MIT Technology Licensing Office, we were able to actually license technology and making CONTINUUS a reality. But we also benefit from many other initiatives here at MIT, like the MIT [INAUDIBLE], the [INAUDIBLE] service, the MIT operational labs, and many others which maybe I'd mention right now. But we're trying to make use of this ecosystem to do the best as we can, and this, I think, is pretty unique of what we can find at MIT on the pharmaceutical space.
Obviously, looking about the Silicon Valley on the other side of the coast, there's lots of similar ecosystem and infrastructure, mostly based on IT high tech. But regarding pharmaceutical, I think really we are in the best place in the world to make this business successful.
There are, I would say, quite a few competing approaches. In fact, when you think about what continuous manufacturing means, this can mean actually several things, and now I'm going to explain what that means. Continuous manufacturing can mean a single reactor unit operation that runs continuously, or some company use continuous manufacturing to refer a multiple step in the synthesis of an active ingredient. Some other company refers continuous manufacturing for the formulation aspect in a certain drug. So several [INAUDIBLE] doing different things in the continuous manufacturing.
We're trying to distinguish ourself with this by defining our approach as integrated continuous manufacturing, meaning that we integrate chemical operation with formulation in one single solution. That's what really differentiates us to other approaches in continuous manufacture, use of normal process technology that allows end-to-end integration where chemical operation runs together with formulation in one single solution under full automatic control. That's where we think all the benefits are coming for implementing continuous manufacturing.
Just for your reference, more than $1 billion has been invested in the last 10 years by the major pharmaceutical company in these different continuous manufacturing initiatives. So yes, there is competitive effort, but we have taken the longest approach, but the one that will really materialize the real benefits, the full reap of continuous manufacturing.
In this end-to-end continuous process, which I describe as a pipe, you can imagine a series of steps within this. You start with continuous flow reactor, then the product of the reaction can go into a continuous separation process. Then the separation process creates a product that needs to be crystallized, so we have developed a continuous crystallization system. From the crystallization, then you go into continuous filtration and drying. And after the API, the Active Pharmaceutical Ingredient, is dried, then this is transferred directly in your formulation process.
And we have several techniques to produce the final dosage form. Can be through extrusion molding technique, can be through thin film tablets, through electrical spinning. Lots of new techniques that allow to produce final product with several different features which are very flexible and amenable to many pharmaceuticals.
Well, it could be seen like this, but actually, it's more trying to help the overall picture of seeing this process approved. As I said before, having FDA approval will be important, so [INAUDIBLE] actually going to this direction is more important for the industry. There was actually not any problem about seeing this as a competition, but the more we see continuous manufacturing trying to be implemented in the pharmaceutical industry, this is beneficial for everyone, including Novartis, ourself, and other companies trying to move toward this technique.
Novartis has a non-exclusive license to use all the technology that comes out from MIT on a free license basis. We as CONTINUUS, we pay a license from MIT to actually use this technology, and we have an exclusive deal with MIT only for our company. So this technology, if you like, is exclusive to Novartis and to Continuous Pharmaceutical.
[MUSIC PLAYING]