Inkbit
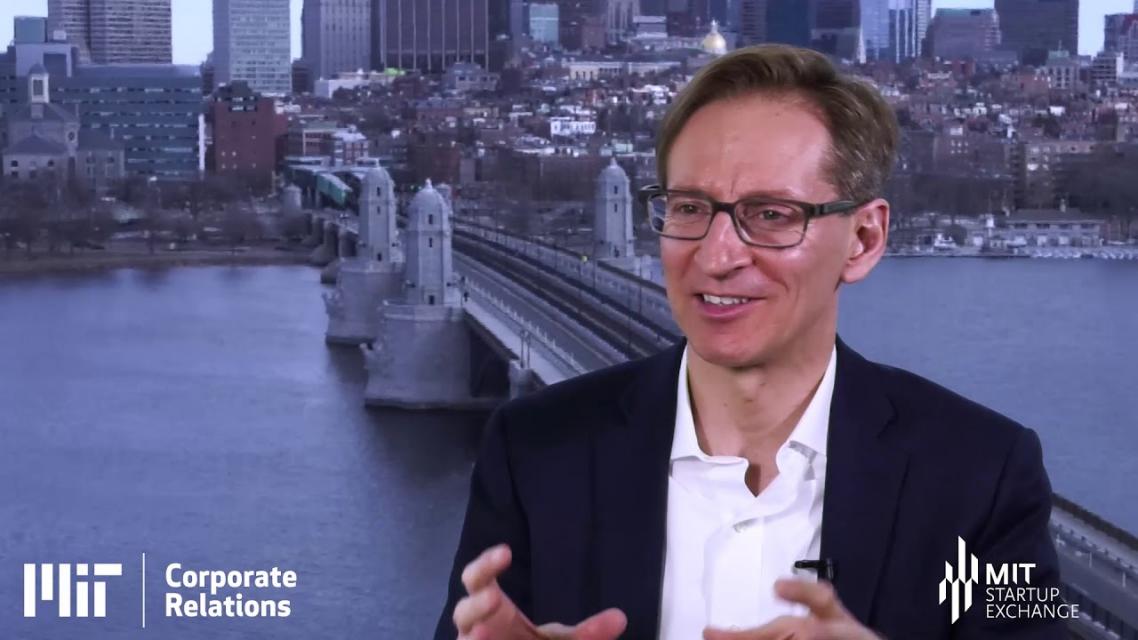
-
Interactive transcript
DAVIDE MARINI: My name is Davide. I am from a small town in northern Italy. My parents had a bakery. So I learned business from them. And I graduated in industrial engineering from Polytechnic of Milan.
I then started my career in London as an investment banker, which I enjoyed very much. But I wanted to apply engineering to something more exciting and more useful. So I decided to come to MIT for graduate school. So I got my PhD in the Department of Mechanical Engineering with a focus on biomaterials. And then I started then my second career in the area of cardiology at Children's Hospital. So I was a researcher. And once again, I developed nanomaterials for biomedical applications.
Then with a friend, also from MIT, I started my first startup company called Firefly. And we developed a multiplex diagnostic platform that was based on micro-fabricated particles that were individually encoded.
The company was acquired. And then I came back to the field of entrepreneurship. And I was introduced to the team that invented the technology behind my current startup, which is Inkbit.
So the team had been working for several years in the Department of Computer Science and Artificial Intelligence under the guidance of Professor Wojciech Matusik. And so Wojciech also is an MIT graduate. And his vision is to marry the field of computation artificial intelligence with the field of manufacturing. The long-term goal is to obtain fabrication systems that are fully automated, and that can learn from their own mistakes, and become better and better over time. So that's also the vision behind Inkbit.
So we have built the first 3D printer with eyes. So we have created an ultra-fast optical tomography scanner that at each layer after the position scans the topography and compares what happened with what was supposed to happen. And if there are any discrepancies, they will be corrected.
So once you have a printer, once you have a machine with a set of eyes, it becomes a qualitative fundamental change in the way 3D printing operates. You can do things that were just not possible before. So at the most basic level, our machine is much more precise, much more reliable, and repeatable than existing machines. We can also integrate external components, external objects inside 3D printed parts.
But most importantly, once you have a machine with eyes, it's the first step for having a machine that learns. So let's say, for example, that you want to use a material that has difficult properties, for example, epoxy, which is a very common material for electronics. Has a tendency to flow after printing. How do you obtain the geometry that you want if your material changes after you have deposited it? The only way, and because we have a set of eyes inside the machine, is to create an artificial intelligence network, a neural network that learns material behavior at every step. It's precisely because we have a scanner, we have eyes, we have a machine vision system integrated into the machine that scans the product in real time that we can allow the machine to learn material behavior at every step.
-
Interactive transcript
DAVIDE MARINI: My name is Davide. I am from a small town in northern Italy. My parents had a bakery. So I learned business from them. And I graduated in industrial engineering from Polytechnic of Milan.
I then started my career in London as an investment banker, which I enjoyed very much. But I wanted to apply engineering to something more exciting and more useful. So I decided to come to MIT for graduate school. So I got my PhD in the Department of Mechanical Engineering with a focus on biomaterials. And then I started then my second career in the area of cardiology at Children's Hospital. So I was a researcher. And once again, I developed nanomaterials for biomedical applications.
Then with a friend, also from MIT, I started my first startup company called Firefly. And we developed a multiplex diagnostic platform that was based on micro-fabricated particles that were individually encoded.
The company was acquired. And then I came back to the field of entrepreneurship. And I was introduced to the team that invented the technology behind my current startup, which is Inkbit.
So the team had been working for several years in the Department of Computer Science and Artificial Intelligence under the guidance of Professor Wojciech Matusik. And so Wojciech also is an MIT graduate. And his vision is to marry the field of computation artificial intelligence with the field of manufacturing. The long-term goal is to obtain fabrication systems that are fully automated, and that can learn from their own mistakes, and become better and better over time. So that's also the vision behind Inkbit.
So we have built the first 3D printer with eyes. So we have created an ultra-fast optical tomography scanner that at each layer after the position scans the topography and compares what happened with what was supposed to happen. And if there are any discrepancies, they will be corrected.
So once you have a printer, once you have a machine with a set of eyes, it becomes a qualitative fundamental change in the way 3D printing operates. You can do things that were just not possible before. So at the most basic level, our machine is much more precise, much more reliable, and repeatable than existing machines. We can also integrate external components, external objects inside 3D printed parts.
But most importantly, once you have a machine with eyes, it's the first step for having a machine that learns. So let's say, for example, that you want to use a material that has difficult properties, for example, epoxy, which is a very common material for electronics. Has a tendency to flow after printing. How do you obtain the geometry that you want if your material changes after you have deposited it? The only way, and because we have a set of eyes inside the machine, is to create an artificial intelligence network, a neural network that learns material behavior at every step. It's precisely because we have a scanner, we have eyes, we have a machine vision system integrated into the machine that scans the product in real time that we can allow the machine to learn material behavior at every step.
-
Interactive transcript
DAVIDE MARINI: So we started operations in June of 2017, and we were initially funded by DARPA, the Department of Defense, and by the National Science Foundation. And we're extremely grateful to those agencies for funding a significant portion of the development of our technology. The first round of funding from investors came in December of 2017, from an Italian company-- so we have a strategic investor-- called IMA. IMA is the world's largest manufacturer of packaging equipment for the pharmaceutical and food industries. So they make extremely high-speed machines that package pharmaceuticals and food-- from teabags all the way to anticancer drugs.
So they are interested into the printing, because if you think about it, it would be considered in the future a more sophisticated form of packaging. In the future, you may want to package drugs in a much more sophisticated way for specific drug delivery purposes, for example. So IMA is, today, the largest shareholder in Inkbit.
We're very fortunate to start life with a very important partnership with Johnson & Johnson, that funded to a great extent the development of our biocompatible materials and of our specific printing capabilities that are of importance to the medical industry. So Johnson & Johnson came to us with a specific product that they wanted to manufacture, but the product was too complicated to build with traditional methods. It has a very intricate geometry and it has to be personalized to each individual.
And they saw, in our system, especially because of the vision system that is integrated into the printer, a way to not only make more reliable, more precise geometries. But also, for FDA approval purposes, having a vision system integrated into the machine is of fundamental importance because our machine can create a digital replica of every product it makes. We talked earlier about the integrated optical tomography scanner that allows us to scan the interior of the part at each layer. So it is very much the equivalent of having a medical CT scan for a product.
So, once this medical device will have to go through FDA approval, Johnson & Johnson believes that having a digital twin of every part will be essential. So that's why they liked our technology. In addition to Johnson & Johnson, we are also developing new products with large corporations in areas as diverse as aerospace and defense, medical, pharmaceuticals, apparels, and automotive. So the ideal customer for us is an organization that wishes to introduce new products that could not be manufactured by traditional methods or wishes to disrupt the way prototyping is made, because with our printer, we can go from prototyping to short-term production all the way to volume manufacturing with the same machine.
We're taking a different approach from the traditional business model of 3D printing, where companies offer equipment, materials, and software. We have found it very rewarding to work side-by-side with customers to help them launch new products faster. Customers have come to us with an idea, and we have helped them in many ways that go far beyond simply printing parts for them. We have developed new biocompatible materials for them. We have at times changed their own design to take advantage of additive manufacturing. And we have helped them by doing small batch production to test the product in the field.
So, in the future, we want to continue on this trajectory by working side-by-side with customers at launching new products faster. So the ideal customer for us is someone that comes to us with an idea, and we help them all the way from designing for additive manufacturing, to small production, material development, all the way to product launch and eventually volume manufacturing.
-
Interactive transcript
DAVIDE MARINI: The source of our competitive advantage is the integrated vision system. It is from the vision system, from the machine learning algorithms that we have developed, that every advantage that we have over the competition emerges.
So the fact that we can print more precisely, more reliably comes from the vision system. The fact that our printer doesn't waste material, unlike competing printers, comes from the fact that it's a contactless technology. So it relies on a vision system. The fact that it creates a digital twin that ensures quality control and traceability of every product comes from the vision system. So we have a number of advantages.
And with respect to the competition, there are a number of players in the industry that today want to launch machines for production. Actually, maybe I'll rephrase this, because some machines for production already exist.
So with respect to the competition, there are a number of machines today that are made for production purposes, not just for prototyping. But as of today, at least, all the systems out there are either single material, or if they are multi-material, they are for prototyping. So to the best of my knowledge, there is no machine out today that can make multi-material parts and is designed for production volume manufacturing. So we are the only one developing such a machine.
The fact that we have an integrated vision system allows the machine to create a digital replica of every single part that is printed. This is very important for a number of reasons. At the most basic level, it allows a customer to track every single product after they have been printed, after they have been shipped to the customer. So let's say that a particular product fails in the field. It would be very important to be able to trace back the history of that single part, no matter how small or inexpensive, and look exactly at how it was printed.
At the higher level, it's very important that a record of every print exists in the files of the company in order to be able to learn from all past manufacturing instances, and establish a learning network to become better and better in the future. So we believe in the idea of an intelligent factory that will learn from its own mistakes, and will become better and better. So that's the vision that Professor Matusik wants to bring to the world.
3D printing has such a potential to disrupt industries that it's not possible to confine it to a single corner. It can disrupt industries as diverse as aerospace all the way to food.
So from our own perspective, we are very passionate especially about the medical industry. But the industries that I think will be disrupted first by 3D printing will be most likely the shoe industry. I can see very easily how shoes will be 3D printed. And there will be no more inventory to be stocked. And each product will be personalized to the athlete.
Another industry that I think will be disrupted will be the eyeglasses industry. I can very well see, in the next five to 10 years, eyeglasses will be entirely 3D printed. There's a company in the Netherlands called Luxexcel. They are already 3D printing lenses, ophthalmic lenses. So from printing glasses to printing the frame and the lens together, the step is not very big. So I would imagine that sector will be disrupted.
Another sector will be personalized medical devices, and in general, every product that could benefit from part consolidation. Instead of injection molding several components and snapping them together later, 3D printing can just really print the entire product in one go. So there are a very large number of areas that 3D printing will impact.
-
Interactive transcript
DAVIDE MARINI: So being part of STEX25 is a great honor. And we're extremely grateful to be selected. MIT has created an amazing community of entrepreneurs, engineers, and visionaries that it reminds me in many ways of Renaissance Florence. It's quite bizarre that I had to come all the way from Italy to relive the atmosphere of Renaissance Florence.
But the atmosphere in Kendall Square is just incredible. Being part of this community is a privilege. And it's a great honor. So I consider myself extremely blessed.
Yes. So ILP has been instrumental for us. Several extremely important conversations that we are having with customers came because of ILP. The program directors helped us tremendously in reaching out to decision-makers at major corporations, and essentially walked us through the process by introducing us to the right people. So for example, we are in the process, hopefully, of selling our second machine to an important customer in France. And that came through ILP.
The traditional model of how you grow a 3D printing company is now well-established. The typical model is sell equipment, sell materials, and sell software. We are a startup. We have a disruptive technology. So we are open to considering different business models that will help customers launch products faster. So in the end, that is what matters.
What we have noticed is that many customers are still a little bit reluctant to adopt 3D printing because of a lack of good materials, lack of repeatability and precision, or simply lack of knowledge of the field. So before they can place an order for the machine, they want to have had a history of interaction with our company.
So what will happen, most likely, is that we will start by expanding internal manufacturing capabilities by offering on-demand manufacturing to customers. And only once a customer feels the need to have their own printer in-house, then we'll provide the printers to them and we'll build out the manufacturing line for them.
But I could easily see a future-- actually, I love fly fishing. So I go fishing on the Quabbin Reservoir. It's in Western Massachusetts. And not far from there, there is a beautiful area. I think it's called North Adams. And you see a lot of awesome brick buildings that are semi-abandoned. Probably they were maybe paper mills or factories that are no longer used.
My dream is to build out the factories of the future around Massachusetts. So we could easily expand and create on-demand 3D printing factories that anybody could use with no need for upfront cost. So let's say-- actually, we just hired a high school student. He just finished high school. And he's taking a gap year. And what I like is the creativity that young age comes with. I can easily imagine a future where high school students will think of new products. And they could launch them and test them in the market with no need of capital.
So in many ways, what I would like to see is the return of the Italian artisan. If you think about the great masterpieces of the past, like Michelangelo and Leonardo, so all those great works of art that we are accustomed to seeing in Florence were the fruit of incredible skill and creativity that was focused on a few products. Well, today, when we think of products, typically, we have lost the touch of the person that designed or made them.
In many ways, I think my dream is to bring back personality into large volume manufacturing, so that maybe in the future we'll no longer think of brands-- typically, when we buy a product, we think of a brand-- we'll think more of the person who designed the product, because once again, 3D printing will allow manufacturing power in the hands of anybody.
-
Interactive transcript
[MUSIC PLAYING]
DAVIDE MARINI: Inkbit is developing the first additive manufacturing system with eyes and brains. We have embedded into our 3D printer a high-speed optical coherence tomography scanner that acquires data in 3D at micron resolution about the parts during printing.
This data enable the machine to create a digital replica of every part that it prints. It also allows us to build machine learning models of the printing process. We use these models to enable 3D printing at higher precision and higher repeatability than is currently possible. Our system can be used to go from a product idea to small scale prototyping, all the way to volume manufacturing on the same machine.