Tulip
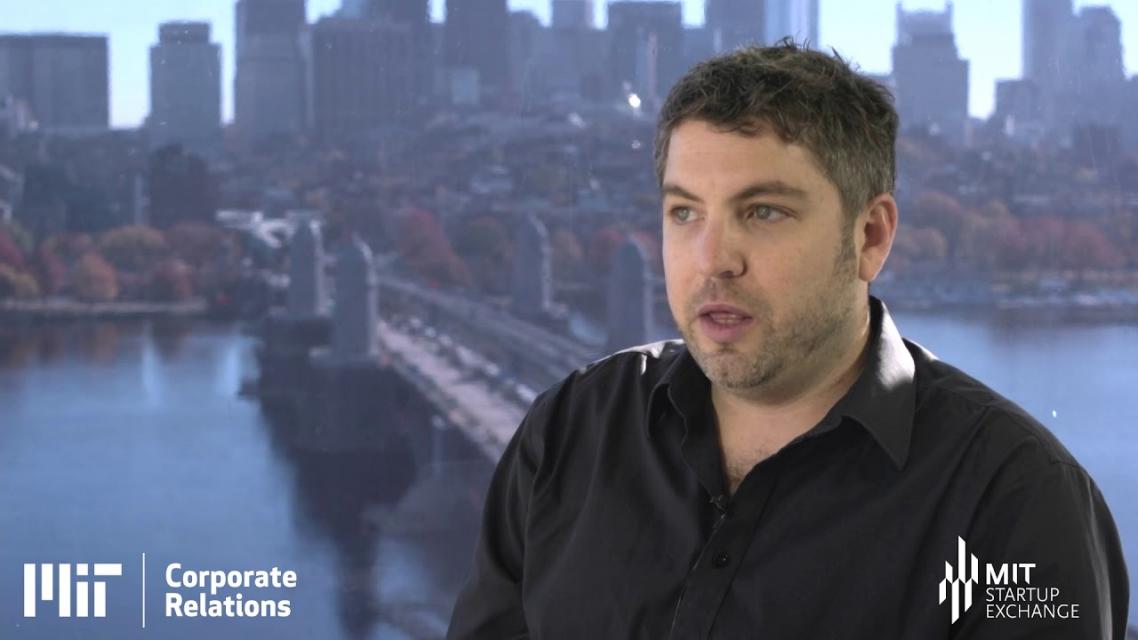
-
Interactive transcript
NATAN LINDER: So I'm Natan Linder. And I'm a graduate of the Media Lab 2011. And I'm a co-founder of Tulip. It's a small MIT startup focused on digital manufacturing, transforming manufacturing floors as we know them today, bringing them to the internet era.
So Tulip is a small serve company out of MIT. And we're focused on helping manufacturing organization transform their process and basically create digital shop floors, which means three things-- we enable people to create what we call software apps much like the apps on your phone that allow you to access data and information and make decisions.
Those apps are helping to guide people through manufacturing process while connecting to sensors and machines on the floors. And those, in turn, provide a host of analytics and information that can be used by anybody who is involved in the manufacturing process and basically implement with usually people called digital transformation, which is a very abstract term that we're actually helping to realize.
So I was a kid who grew up in the '90s with computers all around him originally from Israel-- kind of started my career after my service in kind of big companies like Sun Microsystems and Samsung, got exposed to product development. And by training them, I'm a software engineer embed engineering type.
And I was always attracted to how things are being made. I moved to the US following my wife-- was actually another MIT alum, went to Sloan and decided that I want to try to get into MIT. But I had this little block of time in between the admissions cycles.
So I got introduced to Rod Brooks, who was another great MIT person, we all know. And he fascinated me with his vision for Rethink Robotics. Back then, it was called Heartland. And we started working on building robots that work with people on production lines, which was a really awesome problem to kind of explore.
And then I got into MIT and decided that there's always time to do companies, but not always time to do it MIT. So I kind of went to pursue my degree at the Media Lab working with Professor Pattie Maes at the Fluid Interfaces Group.
And I thought it would be a good pit stop. Only in the process, the Media Lab propels you to rebel. And with Joi Ito at the helm, it was deploy or die. And so we did that and launched Formlabs, which is a 3D printing company.
So that was another very deep exploration into advanced manufacturing additive manufacturing company that built desktops, stereolithography machines, professional grade, yet, that very attainable cost. That went pretty well, and through that working on my PhD, as well-- was working on a fascinating interface problems that happened to interest a bunch of industrial customers or sponsors of the lab.
And they basically started drawing me to their factories when I myself and my research partner, [? Ornie ?] [? Qubot ?] started to spend a lot of time on manufacturing floors. We just saw a much bigger problem at the manufacturing floor at the shop floor level where you have, on one hand, very old backend systems basically antiquated IT.
And on the other hand, you have very sophisticated automation. So robotics and compute machine vision type systems and all sorts of very sophisticated control equipment. And in the middle, there are people who are supposed to kind of connect those two very sophisticated piece of technology. And they're using pen and paper basically, which is mind boggling.
And they're kind of walking around with a supercomputer in their pocket, a smartphone. And it's so accessible. And we all know how to use it. But when they come to work on the production line, whether they're a process engineer, quality engineer, or just the operator doing something, they're just kind of told not to use it.
So they don't communicate the way we take for granted. They don't access information the way we take for granted, et cetera. And to solve that, you need to build a new type of a platform. And that's what Tulip is. It's essentially a manufacturing operating system for the shop floor designed for this internet-driven era. So, and that's what we're building.
[MUSIC PLAYING]
-
Interactive transcript
NATAN LINDER: So I'm Natan Linder. And I'm a graduate of the Media Lab 2011. And I'm a co-founder of Tulip. It's a small MIT startup focused on digital manufacturing, transforming manufacturing floors as we know them today, bringing them to the internet era.
So Tulip is a small serve company out of MIT. And we're focused on helping manufacturing organization transform their process and basically create digital shop floors, which means three things-- we enable people to create what we call software apps much like the apps on your phone that allow you to access data and information and make decisions.
Those apps are helping to guide people through manufacturing process while connecting to sensors and machines on the floors. And those, in turn, provide a host of analytics and information that can be used by anybody who is involved in the manufacturing process and basically implement with usually people called digital transformation, which is a very abstract term that we're actually helping to realize.
So I was a kid who grew up in the '90s with computers all around him originally from Israel-- kind of started my career after my service in kind of big companies like Sun Microsystems and Samsung, got exposed to product development. And by training them, I'm a software engineer embed engineering type.
And I was always attracted to how things are being made. I moved to the US following my wife-- was actually another MIT alum, went to Sloan and decided that I want to try to get into MIT. But I had this little block of time in between the admissions cycles.
So I got introduced to Rod Brooks, who was another great MIT person, we all know. And he fascinated me with his vision for Rethink Robotics. Back then, it was called Heartland. And we started working on building robots that work with people on production lines, which was a really awesome problem to kind of explore.
And then I got into MIT and decided that there's always time to do companies, but not always time to do it MIT. So I kind of went to pursue my degree at the Media Lab working with Professor Pattie Maes at the Fluid Interfaces Group.
And I thought it would be a good pit stop. Only in the process, the Media Lab propels you to rebel. And with Joi Ito at the helm, it was deploy or die. And so we did that and launched Formlabs, which is a 3D printing company.
So that was another very deep exploration into advanced manufacturing additive manufacturing company that built desktops, stereolithography machines, professional grade, yet, that very attainable cost. That went pretty well, and through that working on my PhD, as well-- was working on a fascinating interface problems that happened to interest a bunch of industrial customers or sponsors of the lab.
And they basically started drawing me to their factories when I myself and my research partner, [? Ornie ?] [? Qubot ?] started to spend a lot of time on manufacturing floors. We just saw a much bigger problem at the manufacturing floor at the shop floor level where you have, on one hand, very old backend systems basically antiquated IT.
And on the other hand, you have very sophisticated automation. So robotics and compute machine vision type systems and all sorts of very sophisticated control equipment. And in the middle, there are people who are supposed to kind of connect those two very sophisticated piece of technology. And they're using pen and paper basically, which is mind boggling.
And they're kind of walking around with a supercomputer in their pocket, a smartphone. And it's so accessible. And we all know how to use it. But when they come to work on the production line, whether they're a process engineer, quality engineer, or just the operator doing something, they're just kind of told not to use it.
So they don't communicate the way we take for granted. They don't access information the way we take for granted, et cetera. And to solve that, you need to build a new type of a platform. And that's what Tulip is. It's essentially a manufacturing operating system for the shop floor designed for this internet-driven era. So, and that's what we're building.
[MUSIC PLAYING]
-
Interactive transcript
NATAN LINDER: An operating system for the shop floor. If you think about this metaphor, basically, operating systems have three parts, right? It has the interfaces through which people interact with the system. In our case, they could be tablets or smart phones, they can even be like small buttons or machines that we hook up to the system. It has a driver layer that allows you to connect things to the system, and it has a central processing or a brain, if you like. And that's obviously the cloud in Tulip's world, right?
So the second layer, the driver layer, people use different names for that. We use IoT or industrial IoT. That's the realm this stuff falls into, which is essentially very small inexpensive computers that you can deploy as nodes to the floor, and they provide connectivity to machines or sensors.
And that's sort of a typical sort of IoT statement that I just made. The thing that we do very differently and enabled this operating system is that we want people to just plug and play sensors, whether it's a barcode scanner or an RFID, or just a simple proximity sensor, or it could be a full machine doing surface mount technology type operation and you just want to communicate with that machine.
Those things in our heads are building blocks and they need to have drivers. What the cloud does, essentially, is two things. First, it's an authoring environment that allows you to create those shuffle or apps because an operating system has applications. When you think about an app today, even just the app on your phone, you don't really think about it, but it has some flow, it has some data that it's collecting or you're consuming. And it allows you to do things, for example, talk to your bank, right?
So, typically, developers write those apps and we call them information technology apps or something like that. What is that for manufacturing? There is no tens of thousands of developers that live in that manufacturing space that can sit down and write those apps because there's no real market for that. So what our cloud authoring environment does is allows you to just drag and drop, and very quickly in a PowerPoint style kind create those apps, connect all the different data faucets and links. And basically create a pretty sophisticated app in minutes and deploy it to the floor.
And that app could guide an operator or facilitate a quality assurance process, or can train an individual how to do something, or it can monitor and machine process, and nobody wrote code. And then, because those apps are live and active, you can just hop on the back end and start querying our analytics system. And this is real time analytics, so anything that happens on the floor that a person or a machine or sensor did, you can basically introspect and criss-cross it with a bunch of tools that we've created. And that's pretty powerful. That combination of those apps that the data they collect the sensors and machines they talk to.
And I think that's the core of this idea of an operating system that-- eventually, what will happen to this platform, and the way we're designing it, is that it will be extensible, so we're not we're not doing this right now, but the idea is that the device manufacturers could create their own drivers and certify them for the platform.
Because manufacturing is as big as what humanity does, right? That's, like, what we do, we're a technological species making things. So you can't imagine that one company will be able to know all the things about biopharma and automotive and electronics. So what will happen is various templates for those apps would emerge, so people could very simply say, well, I'm a automotive supply chain manufacturer, and I build this type of widget and this is the best practices to build this type of widget. As opposed to someone using the system to create a process to support drug development in biopharma, for example.
The connecting thread here between those very different industries in this example I just gave you is the fact that is in manufacturing, despite what popular tech press might say, people will remain a dominant factor because people is the most expensive and intelligent computer you would have on your line. It's people who would have the spark to figure out how to make the process better and to manufacture something 2x cheaper. And it's people who would train the next batch of people. And it's people when they're tired and had a bad day that would make the terrible mistake and reduce your quality.
So you have to create-- I think we can agree right now that there's certain things computers and machines do very well and there's certain things people do very well. And I think to have manufacturing that is set for this decade era, whatever, you kind of have to build interfaces for those people in the environments which they do work.
That's why one of the things we're saying is that behind every product there are people. And we don't see that changing no matter what is being made.
-
Interactive transcript
NATAN LINDER: When we meet a production line, it's typical an environment. You can imagine a bunch of benches where manual assembly work or quality assurance steps or some machine outputs are all being handled to carry out a process that turns a final product.
All products have certain set of processes they have to go through as they kind of transform from the parts, raw materials, into a full, shipped product. So when we meet this environment, the first step is to understand that process and what people are actually doing, and then help them instrument it and automate it as much as it makes sense.
So to do that, we have IoT gateways. IoT stands for internet of things. It's a general term. What we mean when we use IoT is simply an edge device that allows you to very quickly-- an easy to plug-and-play sensors and devices and smart tools. This could be a torque gun that would tell you what's the talk of the gun or this could be like a barcode that allows you to scan a certain identifier. This could be a smart thermal camera that watches for some key parameters on the process.
All those different sensors usually require an integrator or somebody to program them in order for them to work. What the Tulip operating system allows you to do is just connect them to this Edge device, and then on a cloud-based interface program their behavior. And this behavior manifests in what we call a shop floor app that basically allows you to very quickly decide the steps in which an operator would go through a process. So that's typically called interactive work instructions.
And the input from the sensor will be collected for the various steps. And this provides tremendous insight into what you told people to do, what they actually did, what their tools and sensors and machines that they have used to follow through the operation-- what data those various devices actually collected. And then, how all of that sort gets integrated to the analytic part of our system, where you can just basically have access to real time information about what's going on the floor, which is a very hard thing to do. Especially because you don't put sensors on people normally.
So if you think about it today, it's like you get very sparse data on the process, typically. And especially in discrete manufacturing that are human intensive by nature, because in discrete manufacturing, that simply means you follow a certain step as opposed to process manufacturing, where you have a food processing factory where 60 tons of potato come in on one side and potato chips come on the other side. Those are basically very sophisticated machines and buildings that are highly automated.
And what we do in discrete manufacturing, where you build an engine or you are a scientist in the lab checking a drug, or if you're an assembler in an electronics factory or stitcher in sports apparel. All of those things are tasks-- they have associated tasks that people actually carry out in those various industries. So things don't come from the magic machine who does x, that does x, you know what mean?
So for those people, basically our operating system should be the way that they interact with their organization, how it helps them do their work, provides them the information to make decisions on their work. When you think about it, it's kind of crazy that basically there's roughly, I think, 12 million people in the United States working in manufacturing. Many of them are on the actual lines and they go into work and you basically tell them, well, you know what? Put your computers away, forget that they exist and just do this thing, like assemble these pieces this way or fill in this form so we can collect the information about that thing.
And that's pretty crazy in 2016. I mean, that is the thing we need to fix. And much like we fixed the way banking works and nobody questions that, or how we shop online and unless you believe there's like an iron dome on this part of what humanity does, then internet is coming in there and will change completely how things are done. And we want to be in the forefront of that.
-
Interactive transcript
NATAN LINDER: Machines that are made today are obviously computers, and they will talk to the world and there's like a whole host of protocols. And the game there, which is certainly important and there's a lot of great companies doing interesting work to collect machine information, analyze it, and then do very smart things on the abundance of data. And some people like to call that big data.
In comparison to that, we're a small data company, right? Because when you're-- we do collect a lot of data but this data doesn't come from machines and spit out information all the time. It comes out from people. And it may come from machines that are 20 years old or something like that, or 15 years old, and they would be sort of obsolete. But, hey, they're doing their job and they're expensive. And they're critical for the manufacturing process.
And they're just using technologies from, like, an era go. How do you get those machines? How do you retrofit them? So with our technology, with the IoT gateways, we can simply connect to their automation equipment, and using the cloud tool environment I described earlier, defined the events that would be supported or that-- basically, take that machine and bring it to the cloud, essentially. Retrofit an old machine and allow it to talk to the cloud.
That's going to be a very important tool to help sort of usher the change. It's not like you're going to completely transform all the machinery in the United States or around the world with a new class of machines overnight because now the internet is important. It's going to be a very gradual process.
And, so, yes. I mean, machines are important and all that kind of stuff, but what's more important is that at end any day, any machine, a million dollar machine or a thousand dollar machine, it's really dumb unless some human comes up to it and tells it what to do. And that is usually a repetitive process that takes time, involves things like preventive maintenance, involves things like all sorts of safety and operation protocols, regulation, things like that. How do you make sure that people are trained and are following procedure while setting up the machines?
So some machines can help operators do that, but many of them, it's like tribal knowledge and muscle memory and that's tough, and those machines are complicated. So I think having to shop for apps to do that is also a pretty interesting area for us, as well.
The nice thing is that our core customer is typically what we call the process engineer. Process engineer is kind of a catch-all term for the quality assurance engineer, industrial engineer, lean engineer, all the different engineers that come together and create the manufacturing process.
So, different engineer need different apps, you know? The quality engineer might need quality data collection, and that's typically done either with automated data point collection using various sensors. I mentioned the thermal camera. It could be machine vision systems that check for specific defects, comparing it visually, like a visual inspection or a CAD comparison. It could be specific gauges or other measurement tools. Imagine a digital caliper that you know you just use it as a caliper and it records the data automatically in the system. So with that, those would be examples of what a quality engineer would use.
The process engineers typically create work instructions. Work instruction is the key document the industry uses to create step by step, you know, here's how you do something. They usually end up as wallpaper. And because humans learn and remember, they just avoid using it. The problem if you follow lean methodology, if you don't use it, you are lowering the chances of you actually finding more value in transforming it to your customer because lean tells you-- and this is sort of the anomaly of lean, that when you find a way to do something better, you need to change your process.
Now, you would agree it's tougher to change wallpaper or static documents. It's easier to change an interactive document that has some sort of a digital thread. So it knows its versions and we have an easy way to collect comments on the process and to share them around. And we obviously have all the bells and whistles of the internet, so we have videos and images and the whole library of symbols and graphics that you can use.
But that's not enough. The biggest thing on the process is that process engineer should decide things like, well, I don't want the operator to click in any information here, I want it to be collected automatically by the sensor and just tell the operator, like, now you scan in a barcode n, now you put this on the scale, and if the scale hits the right number, then you can actually move it to the packing area.
We can speak that and it's well understood because that's how humans think, we kind of think in constructs that, if first you do this and if this happens, you do that. It's kind of like a flowchart. But if you want to codify it, basically your option is hire a programmer or a developer, or your engineer train somebody, the human to be the computer and make those decisions. Or we build those apps that I'm telling you about that could guide someone and encode this behavior. And that's basically the crux of interactive work instructions that would guide someone through the process.
-
Interactive transcript
NATAN LINDER: So I can tell you about one interesting case study that we have done with an IoT member company in the biopharma space, which is pretty interesting. So, usually, when they introduce us to the manufacturing environment, there's some problem that the specific operation people are trying to solve. In this specific case, it was trying to train new people, new operators on the line to go through a highly complicated validated and regulated manufacturing process that has a lot of customization in it. And the manuals are like this thick.
And there is no way to really train you unless a very experienced operator and an engineer walks you through and figures out everything that you're doing. And so what we needed to do is introduce our systems to-- it's very real world, it's like here is like your bench in a factory and go. And so we have to very quickly deploy our technology into this environment.
The fact that we're using off-the-shelf type of interfaces, like touchscreens and tablets and internet infrastructure makes it easy. So deployment was very quick we were able to do it really quickly and developed using our system at full process to train people how to build this specific product. The product was some sort of a liquid purification device that if you get if you get it wrong, it's just not going to work or not going or something like that.
And what was interesting is that I think we managed to introduce a very high double digit reduction in training time. So that a person would be going through training with a human operator to take him through the first steps, but after that, they have to go through sets of consecutive sort of trial runs, like build one with a human operator. And then to get qualified they had to build something on the order of 10.
So imagine that the before state was, two people had to stand roughly 30 minutes, which is the cycle time for that specific component that they're building. And just start calculating the time. It's like it's two people standing and doing that versus a person who is trained doing that once and then the system takes it from there. So that's tremendous if you think about that at scale.
So that's just one story of a concrete benefit that we've seen through pilots that we've conducted. And it's just it's just exciting because I think that where manufacturing is going, it's obviously going to remain very much mass production, we're making a lot of the same thing, but it's also going to be built to order and customized to order. Which means our factories need to become much, much smarter, they need to be able to cope with an end consumer essentially customizing the product to a degree that effectively changes the production line.
And so the production line needs to become a flexible production line. And to get a flexible production line you basically need Tulip. Tulip is helping manufacturing organizations transform their production lines. We're doing it by introducing a new type of manufacturing operating system that allows process engineers of all sorts create shelf for apps, interactive work instructions that are inherently enabled with sensing and data collection using our IoT gateway. And that in turn gives you access through our cloud to abundance of information in real time analytics that can help you measure and fine tune your operation.
The ideal partner for us is manufacturing organizations who want to leverage their manufacturing workforce, who want to give tools of this century to the people on the lines and want to enable them to make quick decisions on the fly and want to rely on them to take their production process a step further. And this is a big idea. One of the things that technology does, like make it faster, better, cheaper. And obviously machines and robots and things like that can do a great job.
However, people are not going away and they're going to be the key factor in gaining access to this new type of smart factory to have flexible manufacturing, to have a data driven manufacturing operation. Talking to billions of devices, the internet will take care of that. OK? So we need technology for enabling people and bring computers to where they were kind of left out in the server room, kind of like in the 90s and a left paper to fill in the blank. Well, until guys like us come around and say, hey, we should all be using the technology we're familiar with and accustomed to change this reality, essentially.