
2023-Japan-Foundation Alloy
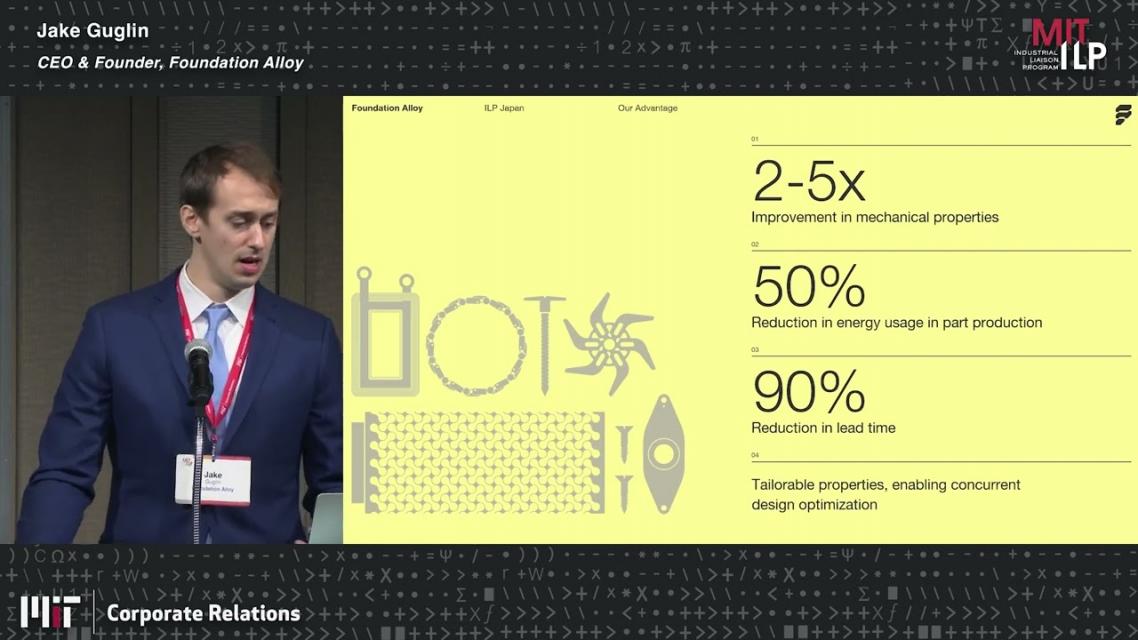
-
Interactive transcript
JAKE GUGLIN: Hi, everyone. Thank you for having us here. Foundation Alloy is enabling modern engineering. With a materials-driven approach to metal part production that provides higher performance parts and a fast, flexible, low-cost supply chain. My name is Jake Guglin. I'm the founder and CEO of Foundation Alloy.
We built this company to provide a platform through better metal parts and supply chains on which engineers and inventors can build the future of industry. This company stems from materials science research at MIT, resulting in our ability to design alloys from the atomic level up for better performance and better processing. Materials determine the performance of both products and their supply chains.
I saw this while managing operations at a space company, where it became clear that engineering and manufacturing technologies have far outpaced the materials that they rely on. This causes diminishing returns on engineering, despite new tools and a fracturing supply chain that can't keep up with increasingly demanding requests with the same inputs. And these issues exist across industries, costing companies untold millions per year in stunted innovation, scrapped parts, and tied-up capital.
Foundation Alloy addresses this with technology developed over decades at MIT and UC Irvine. Using tools like advanced computational physics and nanoscale characterization, we re-engineer metals for superior performance, but also for superior processing to unleash and expand the real potential of modern engineering and manufacturing technologies. Foundation can produce metal parts with mechanical performance two to five times better than those made with comparable alloys.
But because our metals were created with manufacturing in mind, our parts can also be made in days instead of months with lower energy consumption and lower cost, giving us an advantage in everything from rocket engines to drill bits. And as a bonus, our alloys can be tailored, enabling the concurrent optimisation of parts form, production, and material, increasing both the speed and capability of engineering cycles. And this is all accomplished with no hardware updates.
Instead, we're modernizing the metals, which we're now able to control on an atomic level. We can set out with a target in mind and choose elements to both cause and grow the properties we want in the alloy. This includes things like strength and ductility and critical factors driving manufacturability.
We're able to do this based on discoveries made at MIT and UC Irvine that allow us to create and stabilize microstructures through the entire part production process that were previously impossible to retain. Through this we can achieve entirely new tiers of mechanical properties like hardness and tailor many others. This isn't theoretical. We've successfully used this technology to solve a variety of issues.
In one example, NASA came to us looking for new ways to advance nuclear thermal propulsion capabilities. They needed an alloy that was mechanically high performance at both cryo and high temperatures, that also 3D prints with ease and has advanced radiation-shielding properties, not an easy task. In the lab at MIT, we started with a base element, molybdenum, and used our technology to create an alloy that didn't just meet these requirements but exceeded them.
The resulting alloy has two to three times the hardness of pure molybdenum and can be 3D printed and sintered with standard equipment, a previously impossible feat for this style of material. This combination gives NASA better performance, designability, rapid iteration possibilities, and a cost-effective supply chain with which they can now design the next generations of in-space propulsion systems.
We're excited to bring the same technology to Japan. As an international industrial hub, working with Japanese companies represents a unique opportunity for us as a business, and also for our technology to make meaningful contributions to industry. We are in ongoing conversations with several Japanese companies and are excited to expand our presence in the country in the years to come.
With advantages in performance as well as supply chain costs, speed, sustainability, and flexibility, we're confident we can provide a competitive edge to our Japanese partners. For those interested in working with us, we're actively onboarding customers for low-volume manufacturing pilots, in which we can demonstrate, test, and validate the ability of 3D printing to meet customers' cost and performance requirements. We're also executing alloy development agreements in which we work with partners to develop a high-performance alloy specific to your application.
Lastly, these pilots are all intended to help clear the path towards production-scale supply contracts, through which we can deliver partners a large-scale advantage as we grow. Please come see us at our table and don't hesitate to reach out for more information. My name is Jake Guglin, and with the rest of the Foundation Alloy team, we're excited to power your practical innovation. Thank you.
[APPLAUSE]
-
Interactive transcript
JAKE GUGLIN: Hi, everyone. Thank you for having us here. Foundation Alloy is enabling modern engineering. With a materials-driven approach to metal part production that provides higher performance parts and a fast, flexible, low-cost supply chain. My name is Jake Guglin. I'm the founder and CEO of Foundation Alloy.
We built this company to provide a platform through better metal parts and supply chains on which engineers and inventors can build the future of industry. This company stems from materials science research at MIT, resulting in our ability to design alloys from the atomic level up for better performance and better processing. Materials determine the performance of both products and their supply chains.
I saw this while managing operations at a space company, where it became clear that engineering and manufacturing technologies have far outpaced the materials that they rely on. This causes diminishing returns on engineering, despite new tools and a fracturing supply chain that can't keep up with increasingly demanding requests with the same inputs. And these issues exist across industries, costing companies untold millions per year in stunted innovation, scrapped parts, and tied-up capital.
Foundation Alloy addresses this with technology developed over decades at MIT and UC Irvine. Using tools like advanced computational physics and nanoscale characterization, we re-engineer metals for superior performance, but also for superior processing to unleash and expand the real potential of modern engineering and manufacturing technologies. Foundation can produce metal parts with mechanical performance two to five times better than those made with comparable alloys.
But because our metals were created with manufacturing in mind, our parts can also be made in days instead of months with lower energy consumption and lower cost, giving us an advantage in everything from rocket engines to drill bits. And as a bonus, our alloys can be tailored, enabling the concurrent optimisation of parts form, production, and material, increasing both the speed and capability of engineering cycles. And this is all accomplished with no hardware updates.
Instead, we're modernizing the metals, which we're now able to control on an atomic level. We can set out with a target in mind and choose elements to both cause and grow the properties we want in the alloy. This includes things like strength and ductility and critical factors driving manufacturability.
We're able to do this based on discoveries made at MIT and UC Irvine that allow us to create and stabilize microstructures through the entire part production process that were previously impossible to retain. Through this we can achieve entirely new tiers of mechanical properties like hardness and tailor many others. This isn't theoretical. We've successfully used this technology to solve a variety of issues.
In one example, NASA came to us looking for new ways to advance nuclear thermal propulsion capabilities. They needed an alloy that was mechanically high performance at both cryo and high temperatures, that also 3D prints with ease and has advanced radiation-shielding properties, not an easy task. In the lab at MIT, we started with a base element, molybdenum, and used our technology to create an alloy that didn't just meet these requirements but exceeded them.
The resulting alloy has two to three times the hardness of pure molybdenum and can be 3D printed and sintered with standard equipment, a previously impossible feat for this style of material. This combination gives NASA better performance, designability, rapid iteration possibilities, and a cost-effective supply chain with which they can now design the next generations of in-space propulsion systems.
We're excited to bring the same technology to Japan. As an international industrial hub, working with Japanese companies represents a unique opportunity for us as a business, and also for our technology to make meaningful contributions to industry. We are in ongoing conversations with several Japanese companies and are excited to expand our presence in the country in the years to come.
With advantages in performance as well as supply chain costs, speed, sustainability, and flexibility, we're confident we can provide a competitive edge to our Japanese partners. For those interested in working with us, we're actively onboarding customers for low-volume manufacturing pilots, in which we can demonstrate, test, and validate the ability of 3D printing to meet customers' cost and performance requirements. We're also executing alloy development agreements in which we work with partners to develop a high-performance alloy specific to your application.
Lastly, these pilots are all intended to help clear the path towards production-scale supply contracts, through which we can deliver partners a large-scale advantage as we grow. Please come see us at our table and don't hesitate to reach out for more information. My name is Jake Guglin, and with the rest of the Foundation Alloy team, we're excited to power your practical innovation. Thank you.
[APPLAUSE]