
5.4.22-Startup-Ecosystem-Nth-Cycle
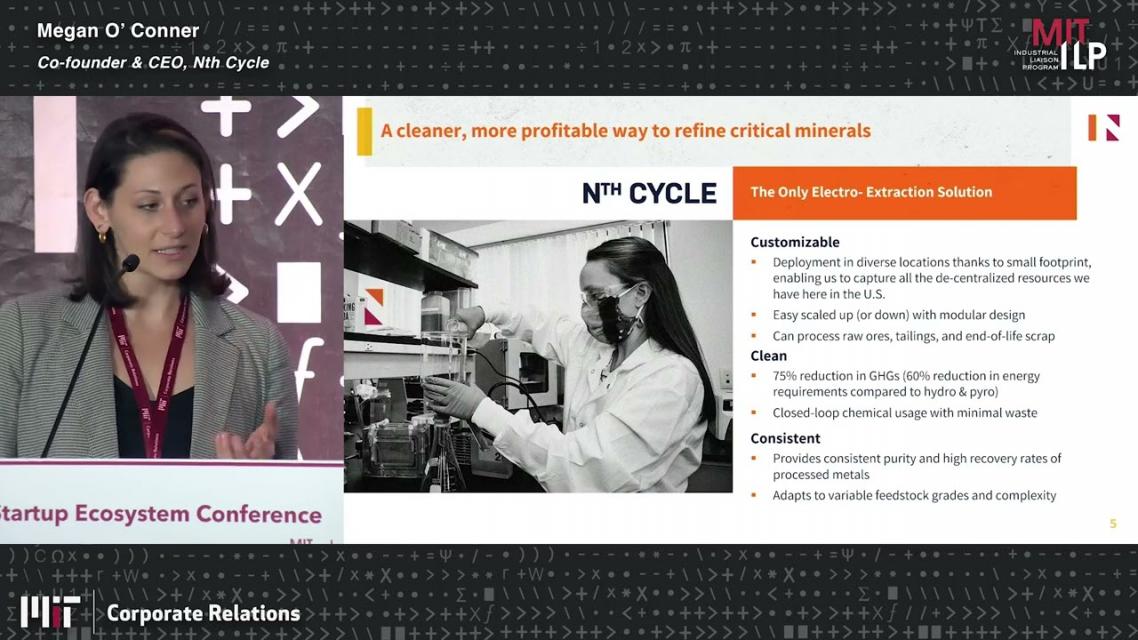
-
Interactive transcript
MEGAN O'CONNER: Hi, everyone. My name is Megan O'Conner. I'm the CEO and one of the co-founders of Nth Cycle. We're developing a new refining technology to get access to all the critical minerals like cobalt, nickel, copper, rare earth metals, that we need to move away from the fossil economy to the clean energy economy. So the main issue that we have with getting all of the critical minerals that we need around the world to make this transition successful is the huge reliance that we have on overseas supply chains.
So even if we start to-- I realize the map is not showing up here. So even if we mine the materials here, 9 out of 10 times these materials have to be shipped over to Asia to be refined into finished or semi-finished products. We then have to buy them back and ship them here again to be used by consumers today.
And then even once we're done with them at their end of life, they're shipped back to Asia to be either recycled or landfilled. So we're losing that valuable material in terms of these critical minerals three times across its lifecycle. So we need to figure out a way to start refining our materials here, so that we can better capture and truly transition in the time frame that we need to.
If we take a look and do a little bit of a deeper dive into the supply chain and where the inefficiencies are, right? We can get these materials like cobalt and nickel from really two different places. We can either start mining more material, or we can start looking at recycled goods or urban mining. Both of these techniques, or I'm sorry. Both of these sources have issues with the different refining technologies that they use.
So both raw ore, so primary ore, and recycled goods have to go through the refining processes of pyro or hydrometallurgy. Both of these techniques are extremely expensive. Think a billion dollars or more to set up these facilities. We currently don't have that capacity here in the States.
And they have extremely high greenhouse gas emissions. So it does not make sense for us to repeat the same issues that we had with fossil over again in the clean energy economy. So this very high cost of processing has truly limited us from becoming self-sustaining here in North America. With the current refining processes being so expensive, not sustainable, and the resources that we have here being very distributed, it's been very difficult for us to have these resources that we need to move forward.
Nth Cycle has developed a technology that can overcome a lot of these inefficiencies that I talked about by being very modular and having a much lower carbon footprint. So our technology is called electro-extraction. So we can refine these materials both from the mining space and the recycling space by having our device on site.
So we can go right to a mine operator. We can go right onto a recycling facility site, eliminating the need to transport all of these materials to these large, centralized facilities, while being more efficient by reducing cost, and again, the greenhouse gas emissions associated with getting these materials out and into the supply chain in the first place. So we can install at the end of a recycling process, the beginning of a mining process, or as the core technology to a lot of the other waste streams that we have here in North America that we haven't been able to tap into before.
So electro-extraction, I like to say has the three C's. It's customizable. It's clean. And it's consistent. So as I mentioned in the previous slide, we can deploy this technology all across the supply chain in the mining, refining, and the recycling space. It's easily scaled up or down with our modular design.
And so it's clean, so we can reduce the greenhouse gas emissions by 75%, and is a completely closed-loop chemical process. We can also provide a very consistent product. So this is critically important, especially when we look at different wastes, right? Typically these wastes, especially if you look at lithium ion battery recycling, you get all of these different cathode chemistries coming in from whether it's from EVs or consumers. We can take all those mixed waste goods and produce a very consistent product that can go directly back into the manufacturing supply chain.
This is what our device looks like today. So we are at commercial scale. It is an electrified, modified filter press. So we've taken this basic idea of water filtration and we've combined it with what's called electrowinning, so applying a specific voltage to this water filtration unit to specifically and selectively remove one metal at a time.
So you can think of your home house Brita filter, right? You have that activated carbon filter in there where you're filtering out all the metals at one time, in that one stage of carbon filter. We've taken that same idea here and we have different carbon filters stacked in series, each with a different electrical current across, so that it selectively removes one metal at a time.
And so that's how our electro-extraction device works. Again, it's very scalable. So we can process four metric tons per eight hour shift per unit. But from there we simply add units in parallel to accommodate the different volumes we'd see, whether it's in recycling or in the mining space.
To give you an overview of an example for the customer working with a feed stock that we look at quite frequently, which is lithium ion battery recycling, we take the lithium ion batteries after they've been shredded into what's called a black mass material. This black mass material is a mixture of the cathode and the anode.
So there's a lot of carbon from the graphite on the anode side, and then the metals that we're after, like the nickel, cobalt, and manganese. We take that waste product, which is currently shipped overseas to be refined. So, again, we're losing that material as it stands today in the supply chain. We go on site with our customers and we process that black mass into the different suite of products, which includes a graphite that can be directly reused in an anode.
We pull out a cobalt and nickel product that can go back into the refining stages for a battery cathode. We pull out a manganese dioxide product which can also be reused in a different type of battery. And then we produce a lithium brine product, which we're working with partners now to refine into a lithium carbonate product.
The quantitative benefits to this process, so again going on-site with these battery recyclers, taking that black mass and upgrading it from a 20% metal content to a 90 plus percent content, increases the sale price from $3 a kilogram to $14 a kilogram. We also significantly reduce the transportation and greenhouse gas emissions by 80%. And then once it reaches that final finishing stage, it reduces the internal OpEx for that facility by 80% as well.
Again, we can provide value at a wide range of locations and supply chain, both at the end of a recycling process, the beginning of a mining process, or as the core technology piece. So today we're looking for partners who are interested in upgrading their existing waste streams or new mining processes. So we're looking for recyclers, new mine developers, OEM, and integrated producers. Thank you.
[APPLAUSE]
-
Interactive transcript
MEGAN O'CONNER: Hi, everyone. My name is Megan O'Conner. I'm the CEO and one of the co-founders of Nth Cycle. We're developing a new refining technology to get access to all the critical minerals like cobalt, nickel, copper, rare earth metals, that we need to move away from the fossil economy to the clean energy economy. So the main issue that we have with getting all of the critical minerals that we need around the world to make this transition successful is the huge reliance that we have on overseas supply chains.
So even if we start to-- I realize the map is not showing up here. So even if we mine the materials here, 9 out of 10 times these materials have to be shipped over to Asia to be refined into finished or semi-finished products. We then have to buy them back and ship them here again to be used by consumers today.
And then even once we're done with them at their end of life, they're shipped back to Asia to be either recycled or landfilled. So we're losing that valuable material in terms of these critical minerals three times across its lifecycle. So we need to figure out a way to start refining our materials here, so that we can better capture and truly transition in the time frame that we need to.
If we take a look and do a little bit of a deeper dive into the supply chain and where the inefficiencies are, right? We can get these materials like cobalt and nickel from really two different places. We can either start mining more material, or we can start looking at recycled goods or urban mining. Both of these techniques, or I'm sorry. Both of these sources have issues with the different refining technologies that they use.
So both raw ore, so primary ore, and recycled goods have to go through the refining processes of pyro or hydrometallurgy. Both of these techniques are extremely expensive. Think a billion dollars or more to set up these facilities. We currently don't have that capacity here in the States.
And they have extremely high greenhouse gas emissions. So it does not make sense for us to repeat the same issues that we had with fossil over again in the clean energy economy. So this very high cost of processing has truly limited us from becoming self-sustaining here in North America. With the current refining processes being so expensive, not sustainable, and the resources that we have here being very distributed, it's been very difficult for us to have these resources that we need to move forward.
Nth Cycle has developed a technology that can overcome a lot of these inefficiencies that I talked about by being very modular and having a much lower carbon footprint. So our technology is called electro-extraction. So we can refine these materials both from the mining space and the recycling space by having our device on site.
So we can go right to a mine operator. We can go right onto a recycling facility site, eliminating the need to transport all of these materials to these large, centralized facilities, while being more efficient by reducing cost, and again, the greenhouse gas emissions associated with getting these materials out and into the supply chain in the first place. So we can install at the end of a recycling process, the beginning of a mining process, or as the core technology to a lot of the other waste streams that we have here in North America that we haven't been able to tap into before.
So electro-extraction, I like to say has the three C's. It's customizable. It's clean. And it's consistent. So as I mentioned in the previous slide, we can deploy this technology all across the supply chain in the mining, refining, and the recycling space. It's easily scaled up or down with our modular design.
And so it's clean, so we can reduce the greenhouse gas emissions by 75%, and is a completely closed-loop chemical process. We can also provide a very consistent product. So this is critically important, especially when we look at different wastes, right? Typically these wastes, especially if you look at lithium ion battery recycling, you get all of these different cathode chemistries coming in from whether it's from EVs or consumers. We can take all those mixed waste goods and produce a very consistent product that can go directly back into the manufacturing supply chain.
This is what our device looks like today. So we are at commercial scale. It is an electrified, modified filter press. So we've taken this basic idea of water filtration and we've combined it with what's called electrowinning, so applying a specific voltage to this water filtration unit to specifically and selectively remove one metal at a time.
So you can think of your home house Brita filter, right? You have that activated carbon filter in there where you're filtering out all the metals at one time, in that one stage of carbon filter. We've taken that same idea here and we have different carbon filters stacked in series, each with a different electrical current across, so that it selectively removes one metal at a time.
And so that's how our electro-extraction device works. Again, it's very scalable. So we can process four metric tons per eight hour shift per unit. But from there we simply add units in parallel to accommodate the different volumes we'd see, whether it's in recycling or in the mining space.
To give you an overview of an example for the customer working with a feed stock that we look at quite frequently, which is lithium ion battery recycling, we take the lithium ion batteries after they've been shredded into what's called a black mass material. This black mass material is a mixture of the cathode and the anode.
So there's a lot of carbon from the graphite on the anode side, and then the metals that we're after, like the nickel, cobalt, and manganese. We take that waste product, which is currently shipped overseas to be refined. So, again, we're losing that material as it stands today in the supply chain. We go on site with our customers and we process that black mass into the different suite of products, which includes a graphite that can be directly reused in an anode.
We pull out a cobalt and nickel product that can go back into the refining stages for a battery cathode. We pull out a manganese dioxide product which can also be reused in a different type of battery. And then we produce a lithium brine product, which we're working with partners now to refine into a lithium carbonate product.
The quantitative benefits to this process, so again going on-site with these battery recyclers, taking that black mass and upgrading it from a 20% metal content to a 90 plus percent content, increases the sale price from $3 a kilogram to $14 a kilogram. We also significantly reduce the transportation and greenhouse gas emissions by 80%. And then once it reaches that final finishing stage, it reduces the internal OpEx for that facility by 80% as well.
Again, we can provide value at a wide range of locations and supply chain, both at the end of a recycling process, the beginning of a mining process, or as the core technology piece. So today we're looking for partners who are interested in upgrading their existing waste streams or new mining processes. So we're looking for recyclers, new mine developers, OEM, and integrated producers. Thank you.
[APPLAUSE]