
2.28-29.24-Ethics-Atacama-Biomaterials
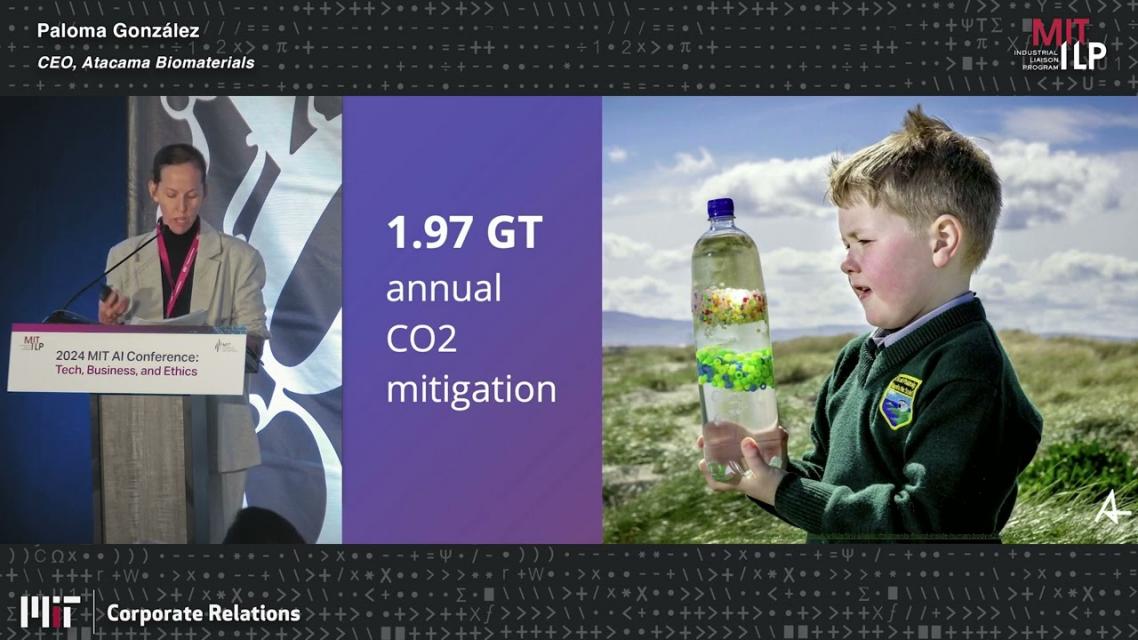
-
Video details
Accelerating Zero-Carbon Powered by Robotics and AI
-
Interactive transcript
PALOMA GONZÁLEZ-ROJAS: Hello, everyone. I'm excited to be here I am Paloma González-Rojas, cofounder of Atacama Biomaterials. I have a master's, a PhD from MIT in machine learning, and a postdoc in chemical engineering. We develop low-carbon materials powered by robotics and AI. We named the company after the Atacama Desert, which is in this picture.
Unfortunately, it looks like this right now. This horrific reality repeats all over the world and inspired us on a life mission. We develop sustainable plastic replacements from diverse local raw materials with a zero-carbon footprint. The current packaging problem builds upon three major challenges, a need for sustainable materials, the disruption of global supply chains, and a material development industry that is unable to keep up with the needed rate of change.
Climate change, pandemics, geopolitical challenges shifting consumer preferences that demand new products requires us to rethink how we develop materials. At Atacama, we believe that the recent technological advancements in AI and robotics are the key to accelerate the development of sustainable materials that rely on regionally available resources, shortening time to market and building flexible supply chains.
Atacama built an AI robotics platform that delivers tailored material formulations in just three months. It optimizes variable biomass to minimize cost and ensure performance and impact of our materials. One fascinating aspect is how AI is changing the nature of work in manufacturing. For example, our robot operators are also data collectors requiring new competencies and uplifting their roles. It is a substantial change in the nature of the workforce in manufacturing that Atacama is driving.
So Atacama replaces plastics, specifically packaging, with low-heat composites from regional biomass. For the 10 years that I researched AI at MIT, I learned the value of acceleration tools. During my postdoc, I did generative molecular engineering, molecular dynamics with my model, which gave us the knowledge to build Atacama's AI.
Atacama's AI enhances performance to ensure that our materials comply with our clients' needs. An example of this was our first AI experimentation that increased its tensile strength by 600%. This work has been extended to other properties of the materials that we are developing. Woodpack is our platform material. It's 100% bio-based suite of flexible films. Its certified paper is recyclable and biodegradable.
Woodpack is uniquely manufactured with low energy through an electrified plasticization. It's cost-effective and price-competitive with conventional plastics. With a global deployment of Atacama's materials, we aim for a 2-gigaton CO2 mitigation by 2035. Woodpack was validated through a pilot with Roche Pharmaceuticals in Latin America. We started replacing traditional polybags with Woodpack in their logistics operations. Then we scaled into packaging for the large medical devices.
This success led us to apply our AI platform into tailoring a specific formulation of Woodpack for cold chain logistics in just three months. This formulation is validated and is currently going through a certification for the health sector.
This is us-- myself, Paloma González-Rojas, I have two degrees in machine learning and a postdoc in chemical engineering from MIT; and Jose Tomás Dominguez, a mechanical engineer with extensive experience in entrepreneurship. Together, we have won prestigious competitions here at MIT, at Dassault Systemes, and at Harvard.
In our team, Jose Antonio Gonzalez leads our LatAm lab in Chile. And Steven Kaye is helping us scale our operations, stemming from his experience scaling a billion-dollar factory for the company Our Next Energy. We have advisors from business, the paper industry, robotics, and a network of support.
Atacama is looking for partnerships. Our research shows that we have applications in almost any industry for our packaging products and potentially for our AI applications. If you want to pilot our technology, we're happy to chat during the exhibition. These pilots can be in e-commerce polybags, beauty packaging, food packaging, health care-- I know that lots of people are from health care-- logistics, and industrial logistics. It is time for Atacama to blossom again. With you, we can make a difference today. Thank you.
-
Video details
Accelerating Zero-Carbon Powered by Robotics and AI
-
Interactive transcript
PALOMA GONZÁLEZ-ROJAS: Hello, everyone. I'm excited to be here I am Paloma González-Rojas, cofounder of Atacama Biomaterials. I have a master's, a PhD from MIT in machine learning, and a postdoc in chemical engineering. We develop low-carbon materials powered by robotics and AI. We named the company after the Atacama Desert, which is in this picture.
Unfortunately, it looks like this right now. This horrific reality repeats all over the world and inspired us on a life mission. We develop sustainable plastic replacements from diverse local raw materials with a zero-carbon footprint. The current packaging problem builds upon three major challenges, a need for sustainable materials, the disruption of global supply chains, and a material development industry that is unable to keep up with the needed rate of change.
Climate change, pandemics, geopolitical challenges shifting consumer preferences that demand new products requires us to rethink how we develop materials. At Atacama, we believe that the recent technological advancements in AI and robotics are the key to accelerate the development of sustainable materials that rely on regionally available resources, shortening time to market and building flexible supply chains.
Atacama built an AI robotics platform that delivers tailored material formulations in just three months. It optimizes variable biomass to minimize cost and ensure performance and impact of our materials. One fascinating aspect is how AI is changing the nature of work in manufacturing. For example, our robot operators are also data collectors requiring new competencies and uplifting their roles. It is a substantial change in the nature of the workforce in manufacturing that Atacama is driving.
So Atacama replaces plastics, specifically packaging, with low-heat composites from regional biomass. For the 10 years that I researched AI at MIT, I learned the value of acceleration tools. During my postdoc, I did generative molecular engineering, molecular dynamics with my model, which gave us the knowledge to build Atacama's AI.
Atacama's AI enhances performance to ensure that our materials comply with our clients' needs. An example of this was our first AI experimentation that increased its tensile strength by 600%. This work has been extended to other properties of the materials that we are developing. Woodpack is our platform material. It's 100% bio-based suite of flexible films. Its certified paper is recyclable and biodegradable.
Woodpack is uniquely manufactured with low energy through an electrified plasticization. It's cost-effective and price-competitive with conventional plastics. With a global deployment of Atacama's materials, we aim for a 2-gigaton CO2 mitigation by 2035. Woodpack was validated through a pilot with Roche Pharmaceuticals in Latin America. We started replacing traditional polybags with Woodpack in their logistics operations. Then we scaled into packaging for the large medical devices.
This success led us to apply our AI platform into tailoring a specific formulation of Woodpack for cold chain logistics in just three months. This formulation is validated and is currently going through a certification for the health sector.
This is us-- myself, Paloma González-Rojas, I have two degrees in machine learning and a postdoc in chemical engineering from MIT; and Jose Tomás Dominguez, a mechanical engineer with extensive experience in entrepreneurship. Together, we have won prestigious competitions here at MIT, at Dassault Systemes, and at Harvard.
In our team, Jose Antonio Gonzalez leads our LatAm lab in Chile. And Steven Kaye is helping us scale our operations, stemming from his experience scaling a billion-dollar factory for the company Our Next Energy. We have advisors from business, the paper industry, robotics, and a network of support.
Atacama is looking for partnerships. Our research shows that we have applications in almost any industry for our packaging products and potentially for our AI applications. If you want to pilot our technology, we're happy to chat during the exhibition. These pilots can be in e-commerce polybags, beauty packaging, food packaging, health care-- I know that lots of people are from health care-- logistics, and industrial logistics. It is time for Atacama to blossom again. With you, we can make a difference today. Thank you.